Designing Optimized Aluminum Castings with Fatigue Life Considerations
Casting is one of the oldest-known manufacturing processes that is still in use today. Complex geometries that are difficult to be shaped by other methods, can be manufactured with relative ease, regardless of size. While the process is at least 6000 years old, as much as early human civilizations, it is mostly believed that the Industrial age in the early 18th century onwards saw a rapid increase in the demand for cast products. New machines and foundries were established, making mass production of parts possible and economical.
Today, cast metal products are found almost everywhere, from critical components for transportation vehicles like aircrafts and automobiles, to industrial and agricultural equipment, heavy machinery, home appliances, medical devices etc. Also, the process is very cost effective and efficient for reuse of any leftover materials. Aluminum’s properties of lightweight and strength bring fundamental advantages when cast into parts, resulting in a widespread use across many industries. Automotive is the largest market for aluminum castings, with a stringent need to produce lightweight components. According to The Aluminum Association, cast products make up more than half of the aluminum used in cars. It comes as no surprise that cast aluminum transmission housings and pistons have been commonly used in cars and trucks since the early 1900s.
In addition to advancements in the manufacturing processes, modern simulation methods have also come a long way in aiding companies get a deeper insight into underlying processes and help innovating in competitive environments. Altair provides a diverse toolset for different manufacturing processes, including specific to casting with Click2Cast, Inspire, OptiStruct, and HyperStudy as some of the frequently used applications. Simulation helps foundries with early detection of defects, reduce trial-and-error, hence saving cost and time, gain new insight into what is happening with the underlying process. A great benefit of simulation comes from optimization, so there are opportunities to optimize the process conditions to get quality products.
There are still some challenges remaining with cast parts in service:
Using the optimization-first approach, FÉMALK is uniquely positioned as a Tier 1 supplier to several large OEMs giving the opportunity to collaborate from the very early phases of their development process. “This speeds up our process, because in the past we used an iterative process between CAD and FEM. Now with OptiStruct we can do this faster, because the first step is usually optimization, and the CAD is the final step or needs little refinement”, says Andras Tanos.
An example he presented is an engine suspension mount with a simulation-driven approach from initial concept generation to final shape with optimization as the backbone. The process involves getting the design space, derive the maximum volume from it, put constraints on mass and frequency, and allow the optimizer to come up with multiple proposals. Because this had to be a cast part, split draw directions were used as constrains during optimization. From the multiple proposals available from the optimizer, choose the best design, interpret in CAD and verify the finalized design.
The complete process also had to factor in fatigue requirements during optimization. For the engine mount part, low-cycle fatigue was an appropriate consideration representing typical roadblocks.
“Low-cycle fatigue during optimization is challenging, as it is governed by plastic strains, which are difficult to include in a linear optimization”, noted Tanos. “We needed some simplified calculation which can run during topology optimization also. Luckily, OptiStruct can also calculate fatigue life, using linear static simulation and applying the Neuber’s correction rule, which is a way to somehow convert linear elastic results into elastic-plastic results”.
The process has proven to be successful at FÉMALK. “It works for us very well. Basically it’s a huge success for our company” added Tanos.
Getting right material properties for cast parts in the analysis or optimization is necessary. Since fatigue life criteria is also factored in the optimization problem, not only monotonic stress-strain properties, but also the cyclic stress-strain, and other fatigue related information like strain-life curves need to be generated.
FÉMALK also handled the issue of characterizing material properties with a clever combination of simulation and testing. Measuring monotonic properties is not straightforward when dealing with cast components. The solidification process in the mold introduces a so called skin-core microstructure, making the outside harder than the inside. This means that if you measure tensile specimens machined from a casting, you may have removed this tough skin, leaving with lower yield and tensile strength. A better solution is to cast specimens to the shape of a tensile specimen, and use those in measurements. If you want to be very thorough, you may also analyze the mold filling characteristics with which you produce these specimens, because these also have an effect on material properties. In OptiStruct the fitted stress-strain curve can be given with an equation or in tabular format.
In order to analyze the low-cycle fatigue region, one must do strain based measurements wherein each measurement controls strain which is constant for all specimens and record the stabilized force amplitude and cycle number the specimen withstood without failure. FEMALK constructed the cyclic stress/strain curves by doing these tests, and with some additional regression analysis and curve fitting the strain-life curves were generated for the material. To validate the material parameters, a benchmark test on a more complex casting was performed to obtain fatigue life under various loading conditions. The nonlinear analysis from OptiStruct produced accurate strains that helped correlate final fatigue calculations with test data. “The nonlinear capabilities improved significantly in the last few releases of Optistruct, which made it possible to run a large displacement analysis using bolt pretension loads, frictional contact and elastic-plastic material properties”, said Tanos.
Finally it was important to check the final CAD model for all criteria, strength and fatigue life. The set up for nonlinear analysis in OptiStruct turned out to be straightforward, whether including connection points and contact surfaces or running subsequent small displacement and large displacement methods all-in-one go. Some unique capabilities in the solver impressed Tanos, “what we also did here was that although we had force requirement in two directions, we only had to run the bolt pretension subcase once, and then the analysis goes in two different directions. I do not know any simulation software that can do this.”
Optimized and validated final design meeting feasibility, static strength, and fatigue life requirements with a reduced mass
The final design turned out to be impressive nonetheless. Compared to the predecessor design, there is a considerable improvement in weight reduction and stiffness – 17% lighter, 15% improvement in the NVH performance. On a separate but similar project with the same process, the weight reduction was even more significant – a 25% reduction. “This even surprised our customers because it overshot their expectations” was the concluding remark.
Check out Andras Tanos of FEMALK discussing design of optimized aluminum castings with fatigue life considerations below.
Today, cast metal products are found almost everywhere, from critical components for transportation vehicles like aircrafts and automobiles, to industrial and agricultural equipment, heavy machinery, home appliances, medical devices etc. Also, the process is very cost effective and efficient for reuse of any leftover materials. Aluminum’s properties of lightweight and strength bring fundamental advantages when cast into parts, resulting in a widespread use across many industries. Automotive is the largest market for aluminum castings, with a stringent need to produce lightweight components. According to The Aluminum Association, cast products make up more than half of the aluminum used in cars. It comes as no surprise that cast aluminum transmission housings and pistons have been commonly used in cars and trucks since the early 1900s.
In addition to advancements in the manufacturing processes, modern simulation methods have also come a long way in aiding companies get a deeper insight into underlying processes and help innovating in competitive environments. Altair provides a diverse toolset for different manufacturing processes, including specific to casting with Click2Cast, Inspire, OptiStruct, and HyperStudy as some of the frequently used applications. Simulation helps foundries with early detection of defects, reduce trial-and-error, hence saving cost and time, gain new insight into what is happening with the underlying process. A great benefit of simulation comes from optimization, so there are opportunities to optimize the process conditions to get quality products.
There are still some challenges remaining with cast parts in service:
- Material properties resulting from different skin-core microstructures
- Fatigue life of cast parts (which by nature means failure at the end of service!)
Using the optimization-first approach, FÉMALK is uniquely positioned as a Tier 1 supplier to several large OEMs giving the opportunity to collaborate from the very early phases of their development process. “This speeds up our process, because in the past we used an iterative process between CAD and FEM. Now with OptiStruct we can do this faster, because the first step is usually optimization, and the CAD is the final step or needs little refinement”, says Andras Tanos.
An example he presented is an engine suspension mount with a simulation-driven approach from initial concept generation to final shape with optimization as the backbone. The process involves getting the design space, derive the maximum volume from it, put constraints on mass and frequency, and allow the optimizer to come up with multiple proposals. Because this had to be a cast part, split draw directions were used as constrains during optimization. From the multiple proposals available from the optimizer, choose the best design, interpret in CAD and verify the finalized design.
The complete process also had to factor in fatigue requirements during optimization. For the engine mount part, low-cycle fatigue was an appropriate consideration representing typical roadblocks.
“Low-cycle fatigue during optimization is challenging, as it is governed by plastic strains, which are difficult to include in a linear optimization”, noted Tanos. “We needed some simplified calculation which can run during topology optimization also. Luckily, OptiStruct can also calculate fatigue life, using linear static simulation and applying the Neuber’s correction rule, which is a way to somehow convert linear elastic results into elastic-plastic results”.
The process has proven to be successful at FÉMALK. “It works for us very well. Basically it’s a huge success for our company” added Tanos.
Getting right material properties for cast parts in the analysis or optimization is necessary. Since fatigue life criteria is also factored in the optimization problem, not only monotonic stress-strain properties, but also the cyclic stress-strain, and other fatigue related information like strain-life curves need to be generated.
FÉMALK also handled the issue of characterizing material properties with a clever combination of simulation and testing. Measuring monotonic properties is not straightforward when dealing with cast components. The solidification process in the mold introduces a so called skin-core microstructure, making the outside harder than the inside. This means that if you measure tensile specimens machined from a casting, you may have removed this tough skin, leaving with lower yield and tensile strength. A better solution is to cast specimens to the shape of a tensile specimen, and use those in measurements. If you want to be very thorough, you may also analyze the mold filling characteristics with which you produce these specimens, because these also have an effect on material properties. In OptiStruct the fitted stress-strain curve can be given with an equation or in tabular format.
In order to analyze the low-cycle fatigue region, one must do strain based measurements wherein each measurement controls strain which is constant for all specimens and record the stabilized force amplitude and cycle number the specimen withstood without failure. FEMALK constructed the cyclic stress/strain curves by doing these tests, and with some additional regression analysis and curve fitting the strain-life curves were generated for the material. To validate the material parameters, a benchmark test on a more complex casting was performed to obtain fatigue life under various loading conditions. The nonlinear analysis from OptiStruct produced accurate strains that helped correlate final fatigue calculations with test data. “The nonlinear capabilities improved significantly in the last few releases of Optistruct, which made it possible to run a large displacement analysis using bolt pretension loads, frictional contact and elastic-plastic material properties”, said Tanos.
Finally it was important to check the final CAD model for all criteria, strength and fatigue life. The set up for nonlinear analysis in OptiStruct turned out to be straightforward, whether including connection points and contact surfaces or running subsequent small displacement and large displacement methods all-in-one go. Some unique capabilities in the solver impressed Tanos, “what we also did here was that although we had force requirement in two directions, we only had to run the bolt pretension subcase once, and then the analysis goes in two different directions. I do not know any simulation software that can do this.”
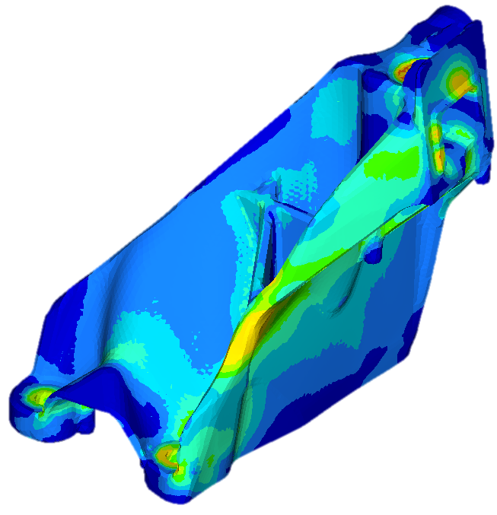
The final design turned out to be impressive nonetheless. Compared to the predecessor design, there is a considerable improvement in weight reduction and stiffness – 17% lighter, 15% improvement in the NVH performance. On a separate but similar project with the same process, the weight reduction was even more significant – a 25% reduction. “This even surprised our customers because it overshot their expectations” was the concluding remark.
Check out Andras Tanos of FEMALK discussing design of optimized aluminum castings with fatigue life considerations below.