How Altair® OptiStruct® Can Help Musical Instruments Sound Better
Stringed instruments with sound boxes, like violins, cellos, and acoustic guitars, generate complex sounds when players strum, pluck, or draw a bow across the instrument’s strings. The sound that action creates then resonates through the instrument’s body, which amplifies its sound. Putting player ability aside, sometimes there are instances where instruments can create unpleasant and unwanted sounds, known as wolf tones.
This auditory phenomenon, named for its wolf-like sound, is a sustaining artificial overtone that can be heard when the pitch of the played note is close to the natural resonant frequency of the instrument body. This process amplifies a specific pitch, creating an unbalanced and oscillating sound, followed by a fast attenuation rate. You’d be forgiven for thinking this happens only because of cheap and poorly made instruments, but the opposite is true. Finely crafted stringed instruments are designed to produce the most resonance possible so they can create a fuller, louder sound. The drawback, however, is that the instrument amplifies wolf tones, too. We decided to reproduce this phenomenon using Altair® OptiStruct®, our modern structural solver with comprehensive, accurate, and scalable solutions for linear and nonlinear analyses across statics and dynamics, vibrations, acoustics, fatigue, heat transfer, and multiphysics disciplines.
First, we created a model of an acoustic guitar along with a vibrating front plate, simplified as a structural model of the solid elements.
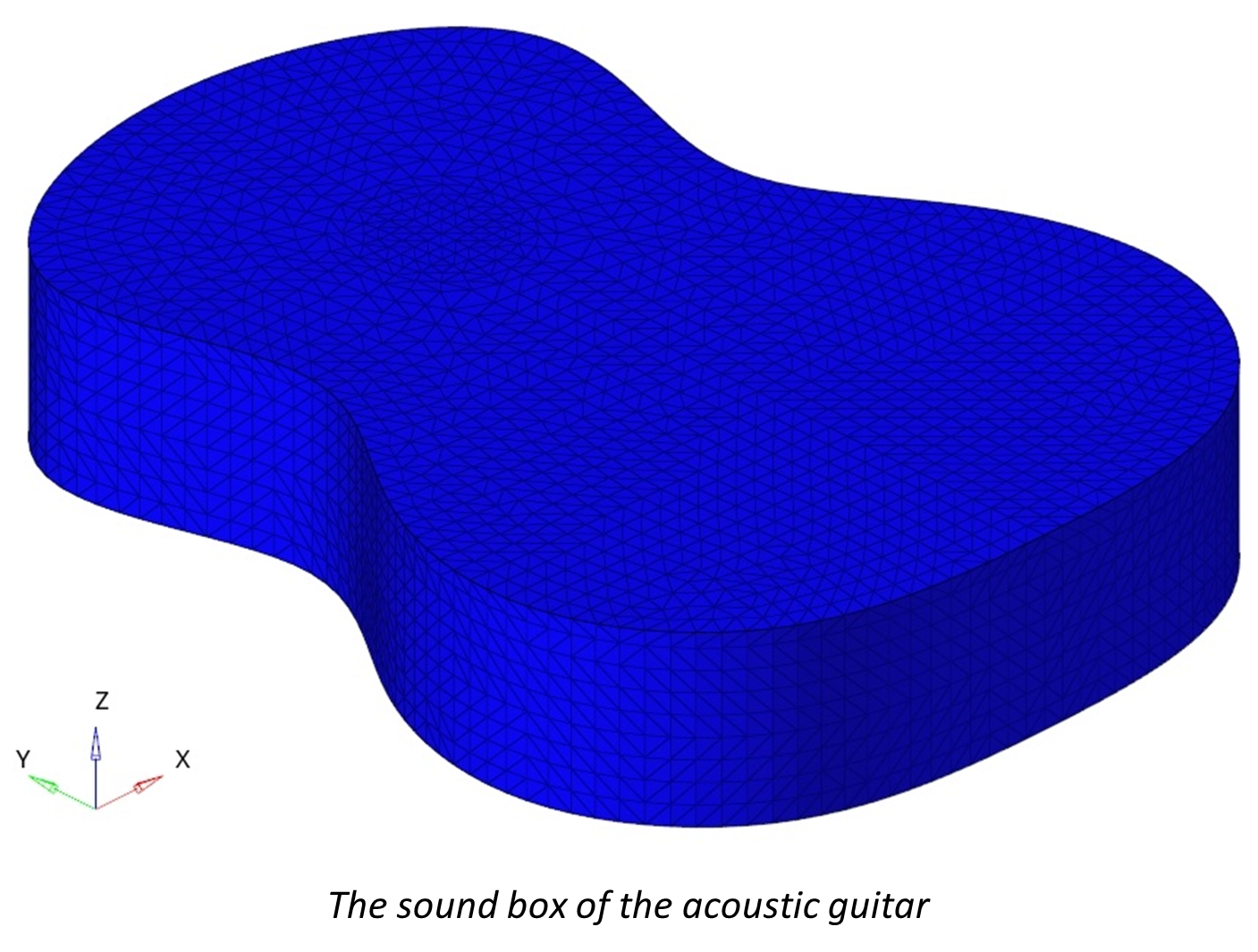
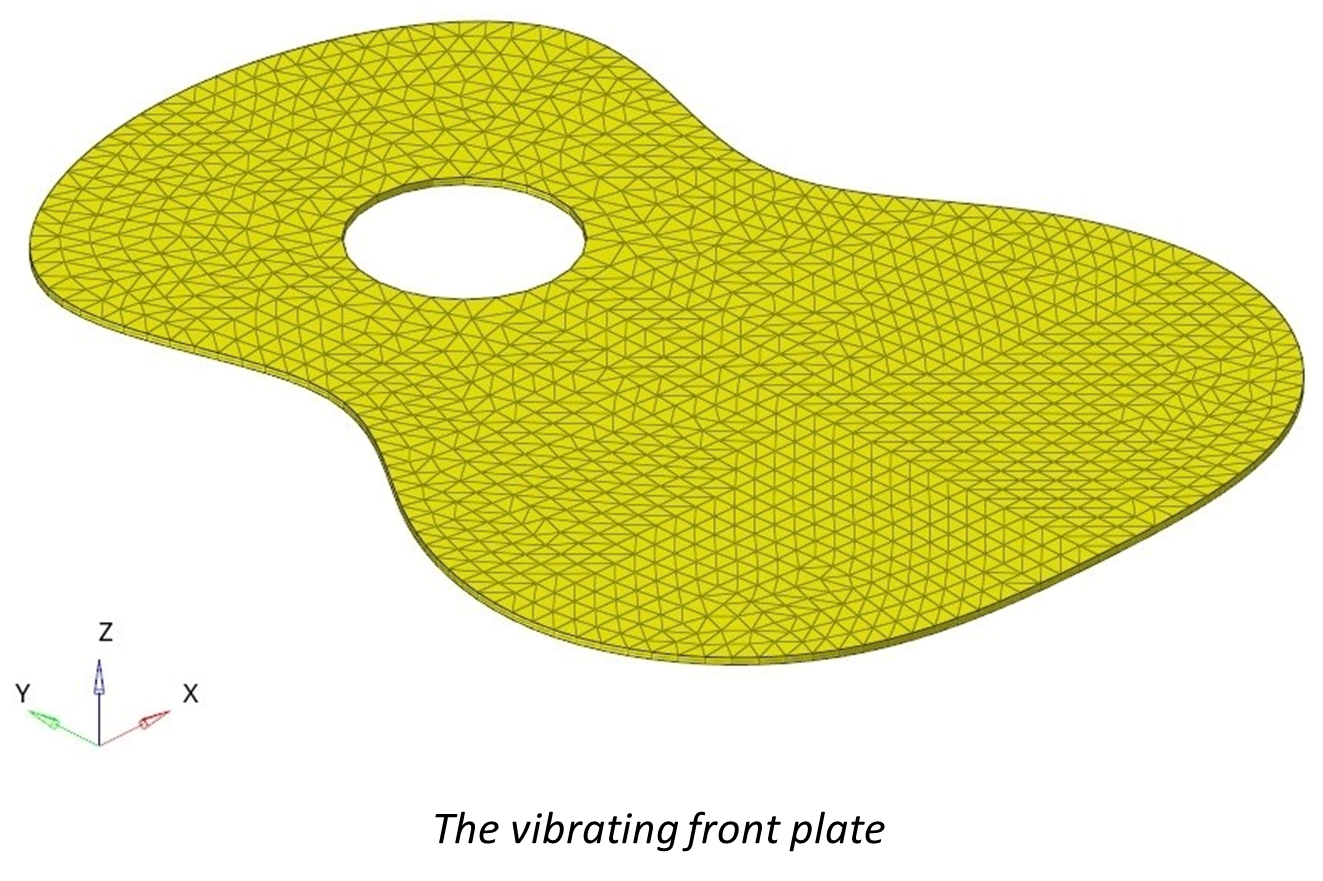
Next, we created a model of a guitar string as a structural model of the shell elements and placed it where you’d find the strings of the guitar.
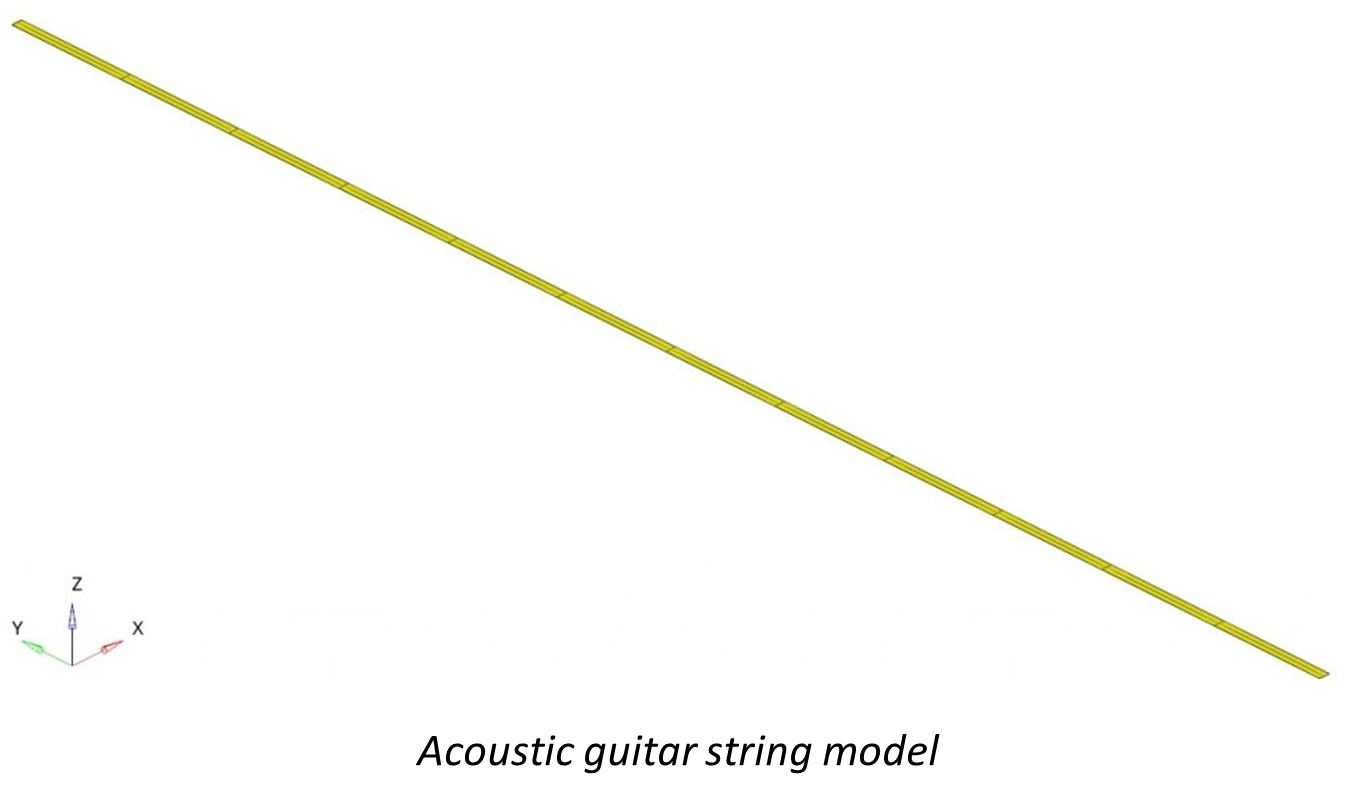
In the external space, we created a spherical acoustic model with a radius of one meter around the guitar model with solid elements. We set an acoustic infinite boundary element on the surface with an evaluation point (to represent a microphone) placed two meters in the vertical direction from the center of the sound hole.
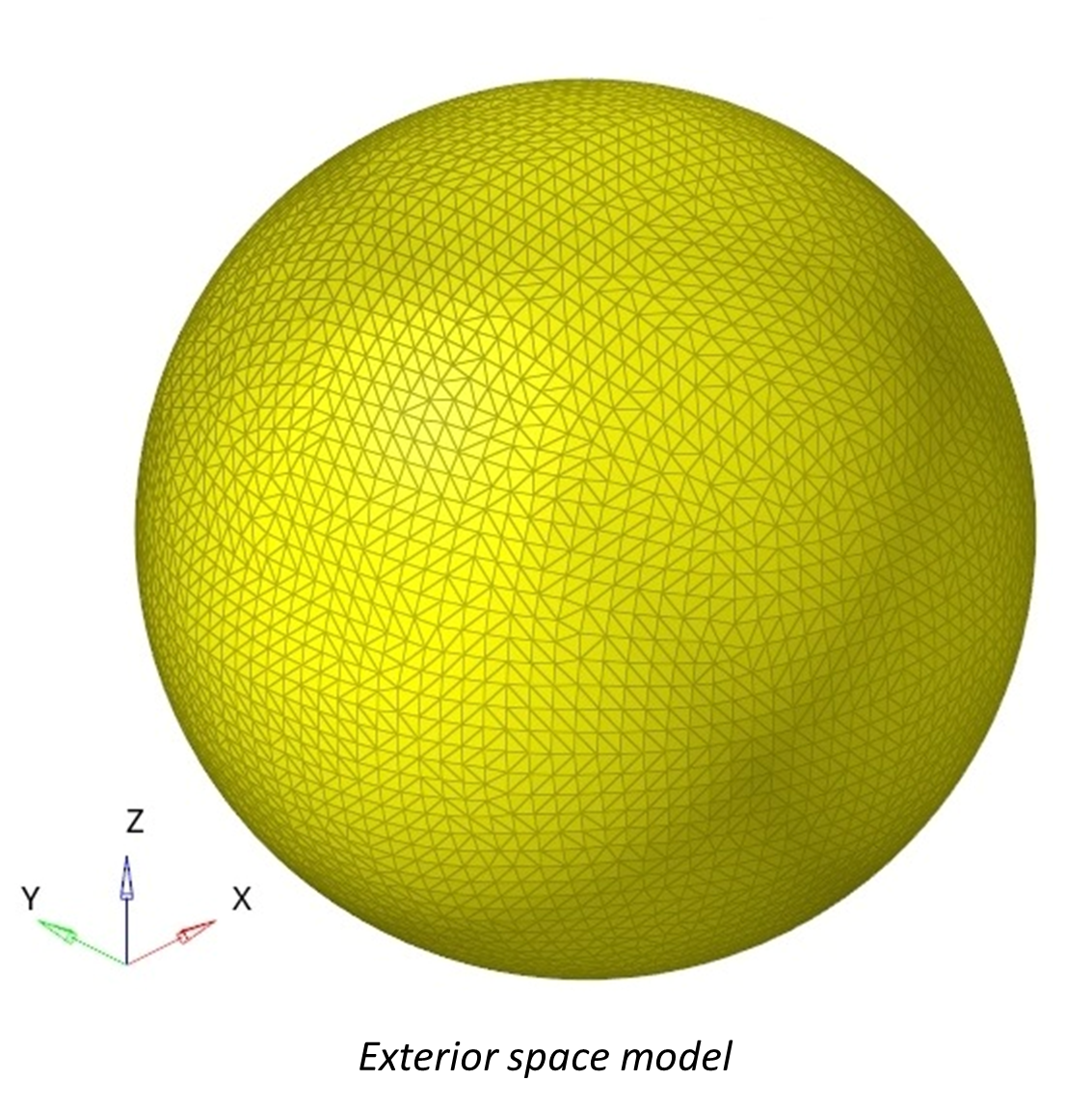
To simulate the behavior of the string after being strummed or plucked, we set a vibration condition; after 0.1 seconds, a load of one Newton is applied to the center point of the string every 0.01 seconds. This simulates the string being played with a guitar pick repeatedly.
When we performed the eigenvalue analysis in advance with the sound box single model, we found that the first cavity resonance mode (Helmholtz resonance) occurred around 150 Hz. As a result, we adjusted the same physical properties of the front plate and strings to about 150 Hz.
In this state, we performed a transient response acoustic analysis using OptiStruct. Under the same conditions, the strings used for this test were set to 134Hz, about one note lower. We then compared the results of both tests by performing calculations with a model where the physical properties were adjusted so they don’t resonate.
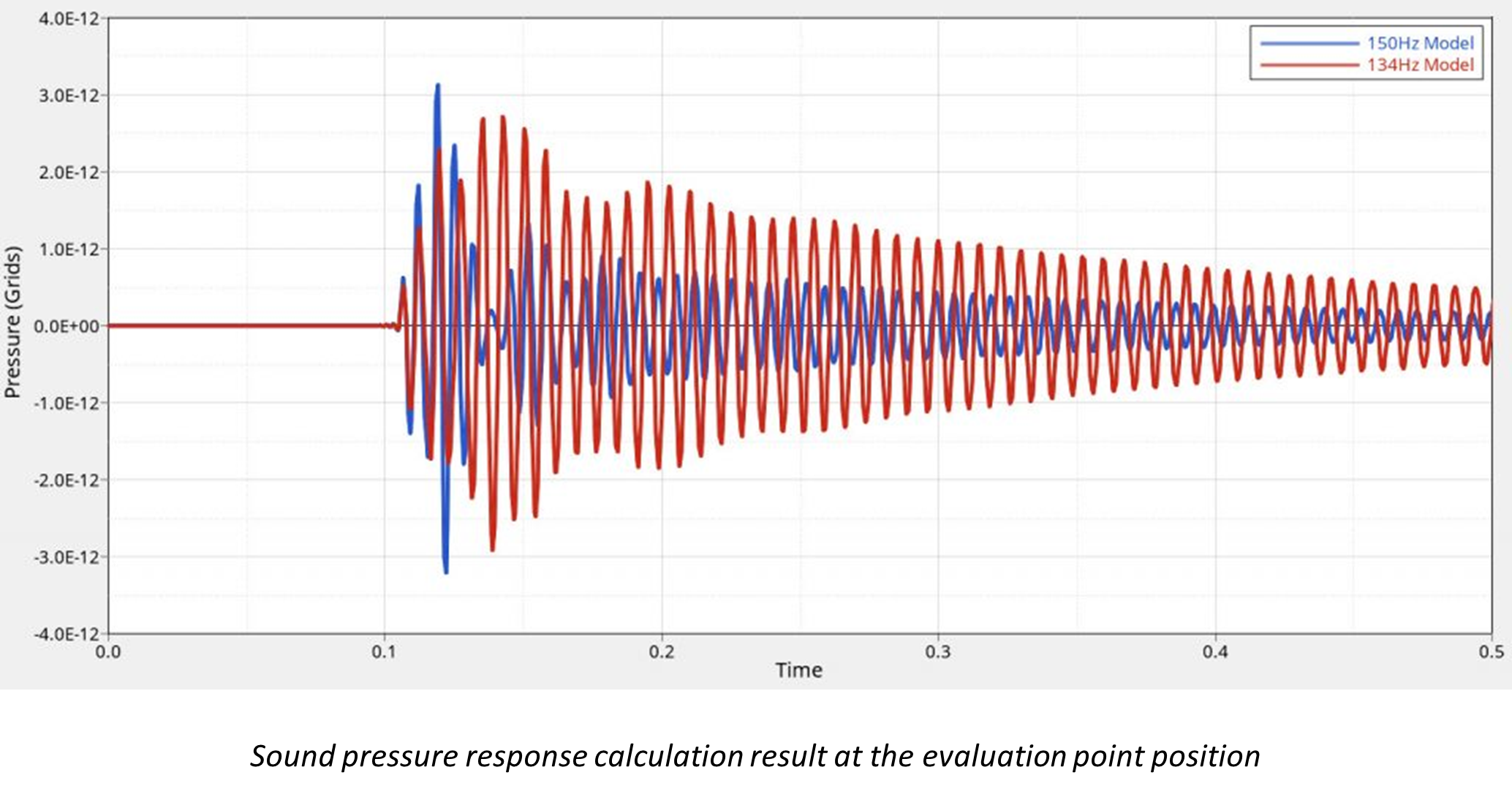
As you can see in the waveform above, when the natural frequency of the string is 150Hz, the sound pressure rises and decays quicker than a frequency of 134Hz. When the instrument’s frequency matches the frequency generated by the string, the resulting wolf tone takes over, becoming louder than the sound of the string vibration itself. It’s thought that wolf tones and those of string vibration cancel each other out, leading to a fast decay.
To expand on this further, we performed the same calculation for a model in which we changed the resonance frequency to 187Hz, representing a smaller, thinner instrument body. While the wolf tone still occurred, it was less pronounced.
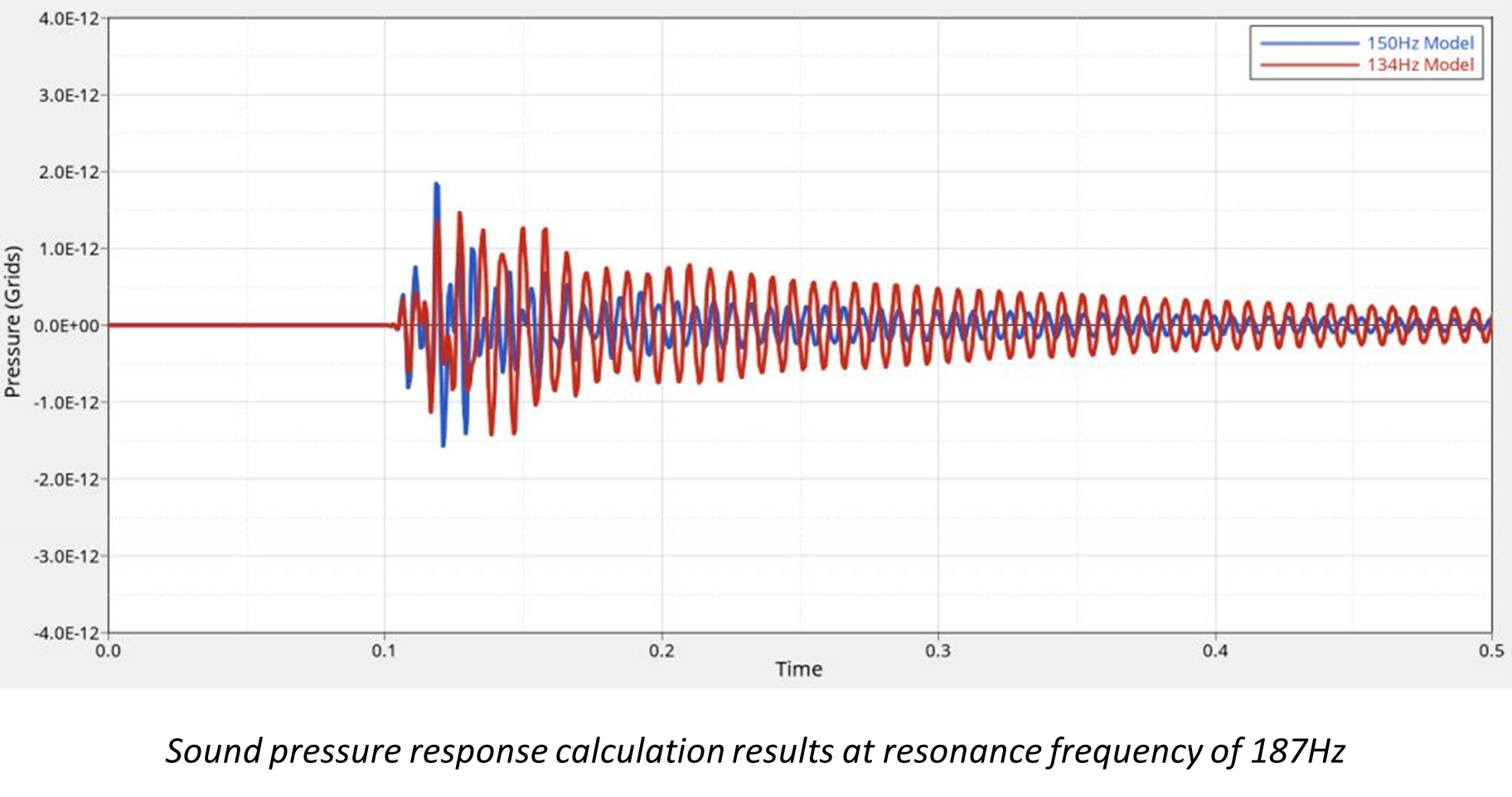
Instrument manufacturers sometimes install wolf tone eliminators comprised of a metal tube and mounting screw with an interior rubber sleeve that fits around the offending string, which reduces the amount of reverberation commonly found on cellos. There are many good wolf tone eliminator products on the market, although a fine-tuning adjustment process needs to be made. Too much dampening and the string doesn’t resonate at all. You can see this in more detail in the video below.
Since it’s structurally impossible to install such a device on an acoustic guitar, manufacturers adjust the natural frequency so it’s between semitones to avoid wolf tones. They do this by arranging a reinforcing material inside the body at the time of production. For the most part, wolf tones aren’t as prominent in acoustic guitars as they are in cellos or violins, but given the instrument’s structure, it’s inevitable it can and does occasionally happen.
By utilizing OptiStruct, we recreated this phenomenon and verified how it occurs. Initial theories about wolf tones describe the air inside the body of the instrument as the reason for the unwanted sound. For this example, we made calculations using only the spatial model of the sound box and the structural model of the strings. We reproduced the phenomenon using this method; however, we couldn’t obtain the same level of sudden attenuation. We found we could achieve this by adding the structural model of the front plate, proving how useful computer-aided engineering (CAE) is when clarifying the root cause of the occurrence.
For the past two decades, OptiStruct topology optimization has driven the lightweight and structurally efficient designs of products you see and use every day. OptiStruct offers many other structural optimization methods and a broad range of essential manufacturing constraints for traditional processes, composites, and additive manufacturing. Learn more about OptiStruct here.