The Implant Boom: It’s Now Hip to Replace Your Hip
The number of joint replacement surgeries in the US is skyrocketing amongst the baby boomer population. Not only are joints being replaced due to fractures and severe pain, but also to facilitate the continuation of an active lifestyle. Previous generations might have reached for their canes, but baby boomers seem to be more likely to grab their running shoes, bikes, or swim goggles.
According to the National Hospital Discharge Survey (NCHS), the number of total hip replacement surgeries of patients 45 years or older in the United States has more than doubled from 2000 to 2010, but the total number of hip replacement surgeries for people between the ages of 45-64 has almost tripled during that same time! This is a dramatic change since many implants used for hip replacements haven’t been designed for active lifestyles. Additionally, much of the data indicating some prostheses should last more than 20 years is based on patients leading a more sedentary lifestyle.
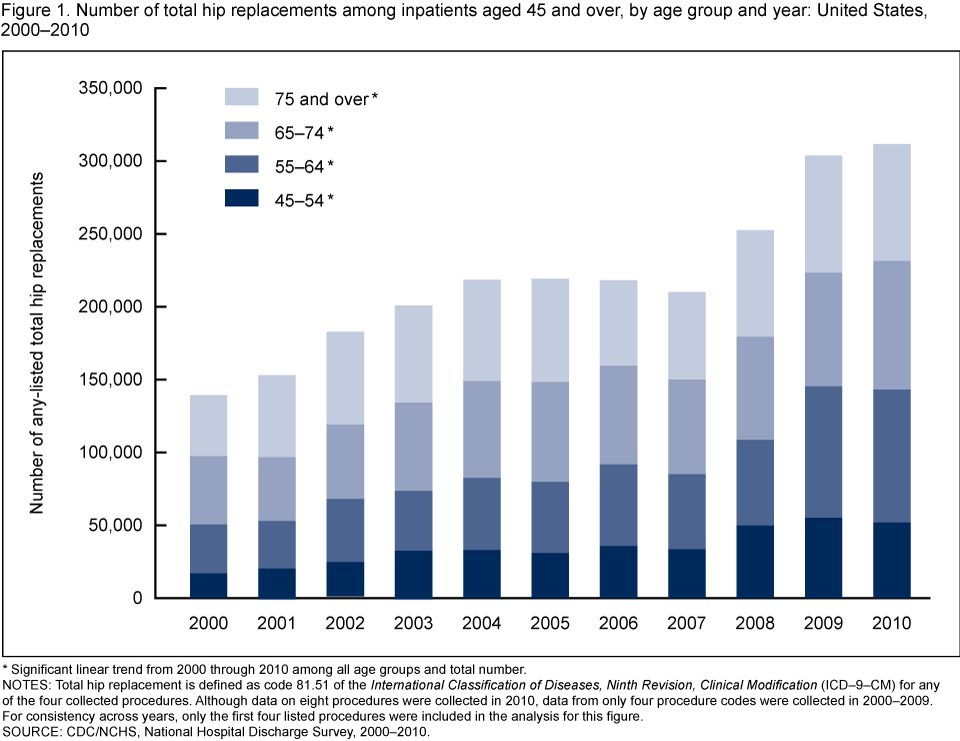
SOURCE: https://www.cdc.gov/nchs/products/databriefs/db186.htm
While total hip replacement surgeries are seeing an increase in demand, 10-20% of the patients may require a revision surgery because of a failure or wearing-out of the prothesis, most commonly due to loosening of the implant stem. This loosening can be caused by bone resorption or loss of bone mass. Revision surgeries can be more complex, especially for elderly patients, and bone resorption can increase the risk of bone fracture. All of this is bad news for younger active patients who will need these prostheses to last several decades.
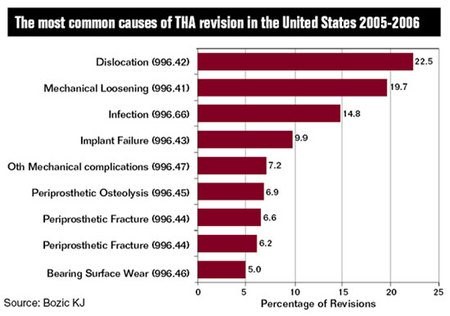
SOURCE: https://www.healio.com/orthopedics/hip/news/print/orthopedics-today
How can these problems be avoided in the future? By applying optimization and simulation technologies and methods to a hip implant can greatly improve the longevity and how it performs. Two ways of doing this are to include more dynamic load cases when designing the hip implant stem and focusing on reducing stress-shielding in the bone surrounding the implant.
When analyzing a design using computer simulation, it is important to include all the various load cases a product might see during its life cycle. The current load cases considered when designing hip implant stems might only involve daily activities such as standing, sitting, walking and climbing stairs. However, with an increasing number of younger patients having total hip replacement surgeries and older patients staying active later in life, additional load cases should be considered. In our study, we included jogging in addition to other standard daily activities, but biking, swimming, and other activities could be included during the design process. Adding these load cases could increase the longevity and performance of hip implant stems.
In considering additional load cases, improving the performance and compatibility with the natural body should also be considered. Most hip implant stems are made of titanium due to its biocompatibility, but titanium is roughly 6.5 times stiffer than the cortical bone of the human femur. When a solid titanium stem is implanted in the femur the load distribution will change in the remaining bone. Often the load into the bone will be reduced because the titanium stem is so much stiffer than the natural bone. This is referred to as stress-shielding. Per Wolff’s law, bone remodels itself to adapt to external loading. With a reduction in loading and stress in the surrounding bone, bone resorption and/or loss of bone mass can occur. Therefore, reducing stress-shielding should help reduce the number of revision surgeries.
Topology optimization optimizes the material distribution within a defined material volume based on the provided load cases, design constraints and objective. This optimization process illustrates where material can be removed and the optimal load paths for the various loads. With the recent advances in additive manufacturing capacities, Altair has introduced lattice optimization which generates structural lattice can be incorporated in areas where the solid structure is not necessary. Each beam diameter of the lattice can be fine-tuned to achieve the design constraints and objective.
These technologies have been applied to the geometry of a general hip implant stem and the results were very promising. The goal of our study was to create a methodology and process to better tune the stiffness and strength of the hip implant stem while including load cases like jogging among the other standard daily activities.
We started by simulating a healthy femur, then a femur with a generic implant and finally a femur with an implant designed using topology and lattice optimization. The optimized prosthesis was designed for metal additive manufacturing which requires careful selection of the print direction, calculating overhang angles, maintaining minimum size parameters and reducing the need for printed support structures.
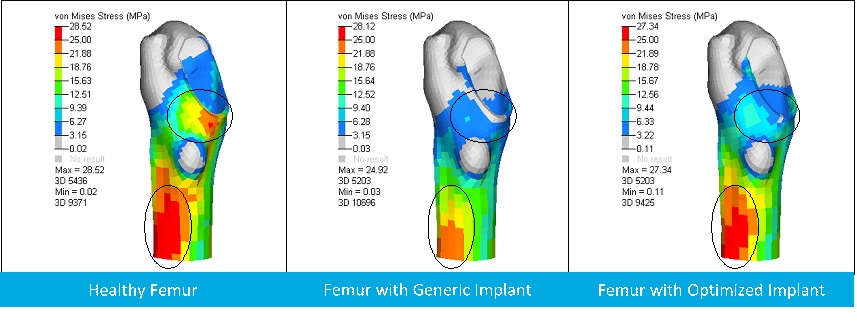
In the end, the stress-shielding caused by the implant was reduced by 57% when comparing the generic design and the optimized design. Furthermore, in the optimized design the stresses in the stem were kept below 575 MPa for all load cases including the jogging and two ISO standard fatigue load cases. For the grade of titanium, the implant was designed for, this would equate to an endurance limit of about 10,000,000 cycles or roughly jogging from Los Angeles to New York and back TWICE!
Coupling this optimization process with additive manufacturing can also provide some very exciting design freedom and customizability of these prostheses. For example, if you are working with a 200-pound male who enjoys water skiing and cycling, specific load cases based on individual activities and physiology could be configured to the optimization process. A customized design could be printed and in the surgeon’s hands the following week!
For more technical information regarding optimized hip replacement technologies, download the white paper here.
According to the National Hospital Discharge Survey (NCHS), the number of total hip replacement surgeries of patients 45 years or older in the United States has more than doubled from 2000 to 2010, but the total number of hip replacement surgeries for people between the ages of 45-64 has almost tripled during that same time! This is a dramatic change since many implants used for hip replacements haven’t been designed for active lifestyles. Additionally, much of the data indicating some prostheses should last more than 20 years is based on patients leading a more sedentary lifestyle.
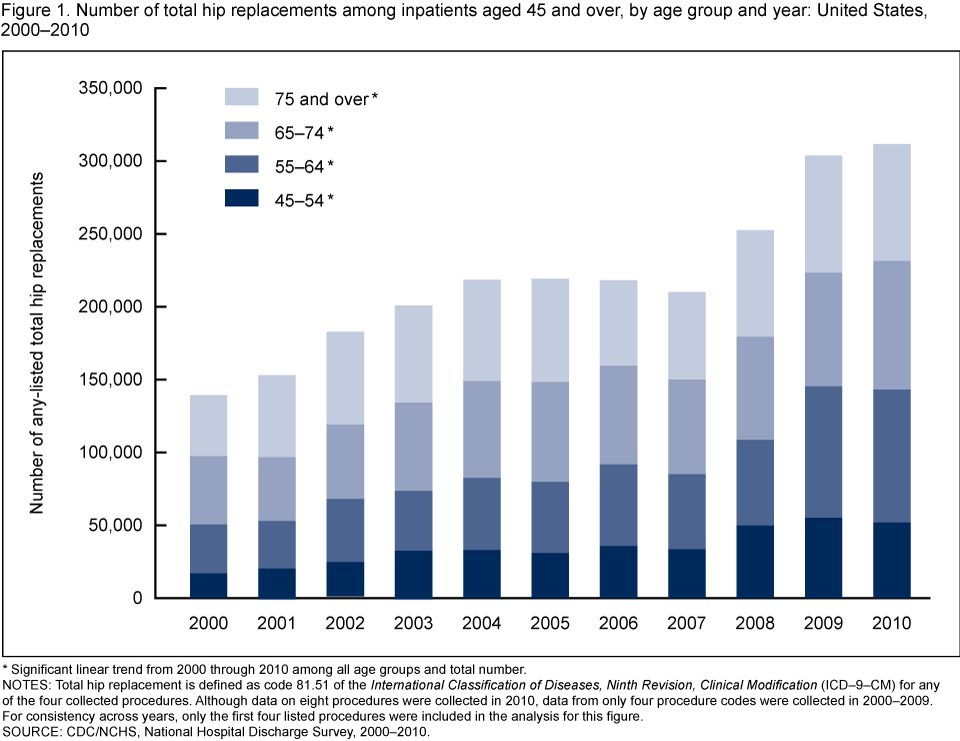
SOURCE: https://www.cdc.gov/nchs/products/databriefs/db186.htm
While total hip replacement surgeries are seeing an increase in demand, 10-20% of the patients may require a revision surgery because of a failure or wearing-out of the prothesis, most commonly due to loosening of the implant stem. This loosening can be caused by bone resorption or loss of bone mass. Revision surgeries can be more complex, especially for elderly patients, and bone resorption can increase the risk of bone fracture. All of this is bad news for younger active patients who will need these prostheses to last several decades.
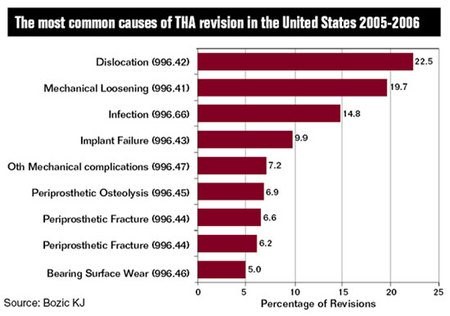
SOURCE: https://www.healio.com/orthopedics/hip/news/print/orthopedics-today
How can these problems be avoided in the future? By applying optimization and simulation technologies and methods to a hip implant can greatly improve the longevity and how it performs. Two ways of doing this are to include more dynamic load cases when designing the hip implant stem and focusing on reducing stress-shielding in the bone surrounding the implant.
When analyzing a design using computer simulation, it is important to include all the various load cases a product might see during its life cycle. The current load cases considered when designing hip implant stems might only involve daily activities such as standing, sitting, walking and climbing stairs. However, with an increasing number of younger patients having total hip replacement surgeries and older patients staying active later in life, additional load cases should be considered. In our study, we included jogging in addition to other standard daily activities, but biking, swimming, and other activities could be included during the design process. Adding these load cases could increase the longevity and performance of hip implant stems.
In considering additional load cases, improving the performance and compatibility with the natural body should also be considered. Most hip implant stems are made of titanium due to its biocompatibility, but titanium is roughly 6.5 times stiffer than the cortical bone of the human femur. When a solid titanium stem is implanted in the femur the load distribution will change in the remaining bone. Often the load into the bone will be reduced because the titanium stem is so much stiffer than the natural bone. This is referred to as stress-shielding. Per Wolff’s law, bone remodels itself to adapt to external loading. With a reduction in loading and stress in the surrounding bone, bone resorption and/or loss of bone mass can occur. Therefore, reducing stress-shielding should help reduce the number of revision surgeries.
Topology optimization optimizes the material distribution within a defined material volume based on the provided load cases, design constraints and objective. This optimization process illustrates where material can be removed and the optimal load paths for the various loads. With the recent advances in additive manufacturing capacities, Altair has introduced lattice optimization which generates structural lattice can be incorporated in areas where the solid structure is not necessary. Each beam diameter of the lattice can be fine-tuned to achieve the design constraints and objective.
These technologies have been applied to the geometry of a general hip implant stem and the results were very promising. The goal of our study was to create a methodology and process to better tune the stiffness and strength of the hip implant stem while including load cases like jogging among the other standard daily activities.
We started by simulating a healthy femur, then a femur with a generic implant and finally a femur with an implant designed using topology and lattice optimization. The optimized prosthesis was designed for metal additive manufacturing which requires careful selection of the print direction, calculating overhang angles, maintaining minimum size parameters and reducing the need for printed support structures.
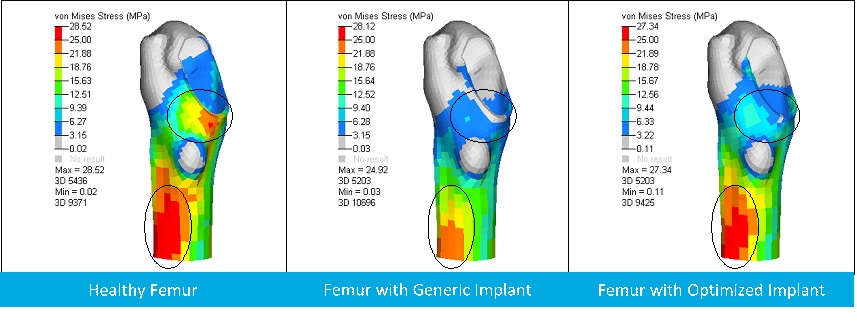
In the end, the stress-shielding caused by the implant was reduced by 57% when comparing the generic design and the optimized design. Furthermore, in the optimized design the stresses in the stem were kept below 575 MPa for all load cases including the jogging and two ISO standard fatigue load cases. For the grade of titanium, the implant was designed for, this would equate to an endurance limit of about 10,000,000 cycles or roughly jogging from Los Angeles to New York and back TWICE!
Coupling this optimization process with additive manufacturing can also provide some very exciting design freedom and customizability of these prostheses. For example, if you are working with a 200-pound male who enjoys water skiing and cycling, specific load cases based on individual activities and physiology could be configured to the optimization process. A customized design could be printed and in the surgeon’s hands the following week!
For more technical information regarding optimized hip replacement technologies, download the white paper here.