Designing Guillotine Valves to Control Mineral Flow Using Altair EDEM
Guest post by Blue Ocean Engineer
Blue Ocean Engineer is a Brazilian company that focuses on the design of innovative solutions in heavy machinery for bulk handling application. To design better and more cost-effective products, Blue Ocean heavily relies on simulation at the conceptual and engineering phase.
Working alongside some of the major players in the mining industry, Blue Ocean has developed guillotine valves that control or completely shut off mineral flow, especially under silos for mineral storage.
The main challenge imposed on the design of such valves is the variation on the normal and tangential forces at the presence of different characteristics of the bulk material. As the valves are a very robust component that handles big materials, any extra weight on the frame of the valve makes it harder to move the hydraulic cylinder forward through the bulk material. Figure 1 shows a regular size guillotine valve frame.
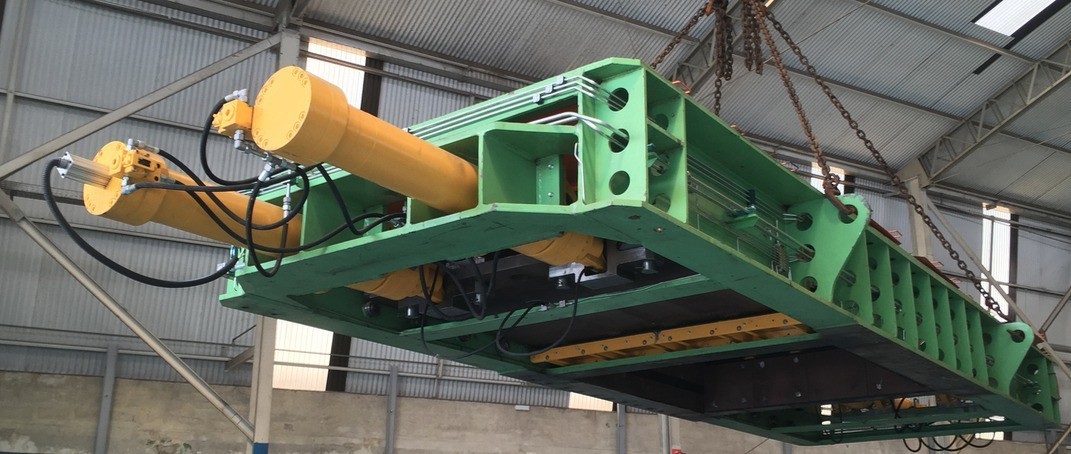
Bulk material characteristics such as grain size, angle of repose, grain size distribution, material shape, slab/sphere ratio, are some of material features that have direct influence on the main loads to which the guillotine valves are exposed. Thus, a big part of this equipment design is to correctly calculate the loads on the process of shutting off the valve, determining the correct size of the metal sheets, which gives the advantage of making the valves robust enough to not make it too heavy, increasing the normal load, and not too soft, compromising the stiffness.
Usually, the task of performing the calculation of the hydraulic forces needed to overcome the bulk material resistance from movement started with declaring a hypothesis about the material packing. Frequently, the hypothesis is that the material is packed and cohesive, which is close to the worst-case scenario of moving the shut off valve against the bulk material.
This hypothesis usually leads to a very heavy shut off valve, and a bigger than necessary hydraulic system. All this to prepare the system to work with a situation that most of the time is not realistic. Figure 2 shows a typical silo application where it is possible to see how material has a large range of grain size distribution, although the hypothesis of very cohesive material does not hold true.
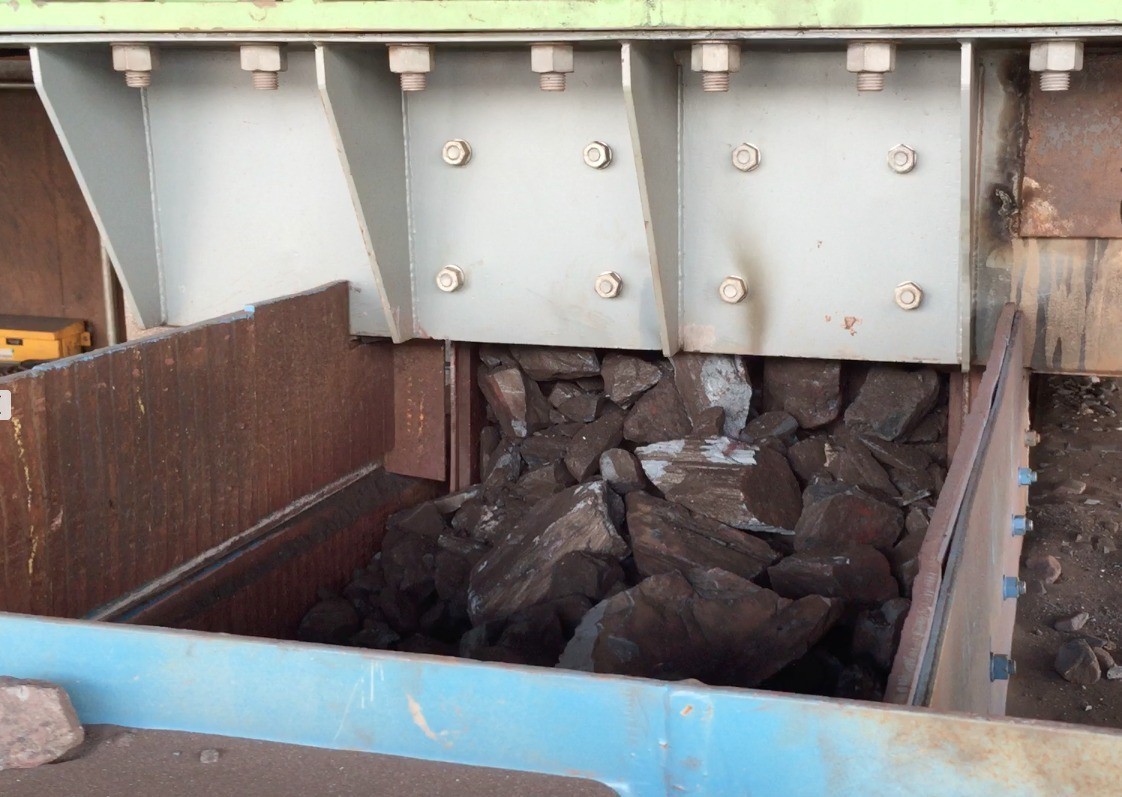
When Blue Ocean decided to use EDEM software to simulate material flow and guillotine valve movement through bulk material it was realized that, in most cases, the real loads upon the valves are much lower than the ones calculated by the hypothesis used to design it. Simulation of various shut off sliding time showed that the maximum load could be reduced by 20%, changing the closing time and blades shut off sliding sequence. Thus, much more reliable and lighter valves could be used, increasing its application and spreading its use.
One example of application for those guillotine valves are in rectangular silos that store Iron Ore. Figure 3 below shows a virtual model of such silo. In this example the blue grains represent a sphere material, that is predominant. Yellow grains are slab material, that were simulated to have in different proportion to sphere material.
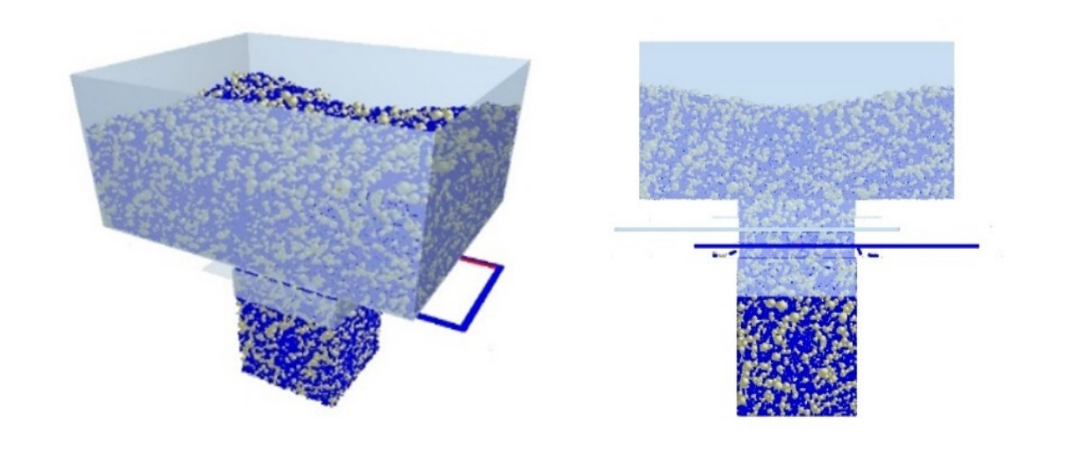
Using an EDEM tangential force report, it is possible to determine the force that the guillotine valve blades will be exposed to, allowing the proper design of the motion mechanism that drives the blades. Also, it is possible to analyze the influence of the grain size distribution, and the proportion of slab / sphere ratio on the tangential force. This kind of analysis is only possible because of the versatile and numerous simulation reports that are built in the EDEM Analyst module.
Other experiments that have been performed include investigating the motions of the blades, such as the linear advance speed (mm/s) and motion sequence, always looking at the tangential and normal forces response for each different process. This permits the design engineers to pinpoint the drive mechanism setup, and field service engineer to perform the correct commissioning tasks to quickly work out the best blade configuration for the required application.
Another important set of information that is feasible to simulate is the wear pattern on the blade’s surfaces. It is possible to work with the wear models using EDEM’s material surface library and out the critical wear out areas that might concern the field service engineer while the equipment is up and running. Figure 4 shows a simulation where those areas have been identified and used to inform the design team. Identifying those areas can significantly improve the blade’s design.
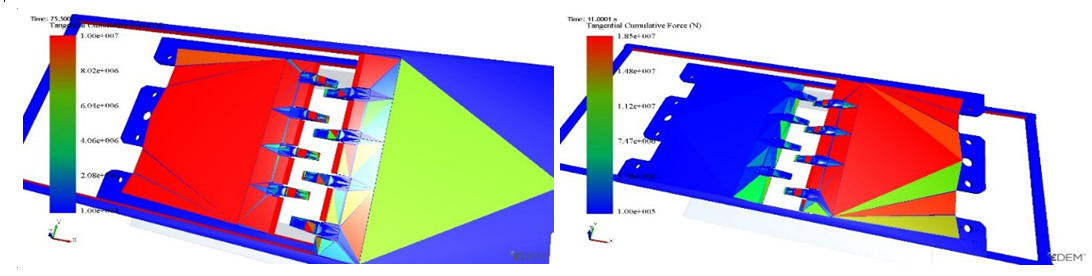
It has been shown that EDEM is a powerful and reliable tool to use in experiments and analyze the forces that the blades are submitted to while working in a set of operation parameters. It allows design engineers, application engineers and field service engineers to look for problems during normal operation as early as the conceptual and design phases. This is a very welcome money saver and it reduces the warranty claims by the user of the heavy machinery.
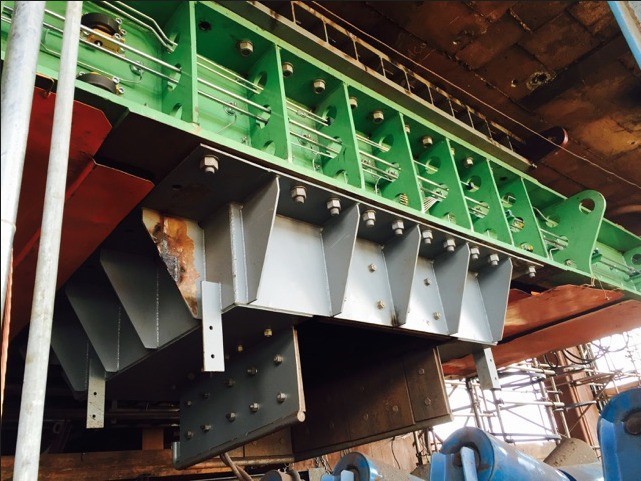
Blue Ocean is very pleased to work with EDEM and prototype their innovative machines with such a tool, figuring out the best solution from the simulation insights.
For more information about Blue Ocean Engineer, visit their website.