Digital Debunking: Could a Dinosaur Really Crush a Jurassic World Gyrosphere?
Recently, under Greenland’s vast ice, scientists discovered what they believe to be a new dinosaur. Now that the third Jurassic World film, "Jurassic World: Dominion" is out, we thought, What better way to honor the occasion than to rewatch some classic dinosaur films over the holidays?
One part of “Jurassic World” that stuck out was the glass gyrosphere vehicles used in the park. In one scene, Jimmy Fallon pops up on the video screen to present a safety demonstration of the gyrosphere as it rolls through a field full of roaming dinosaurs.
We're not sure what’s more concerning: That people are getting in these giant, rolling glass balls to go look at dinosaurs, or that they’re putting their safety into the hands of Jimmy Fallon.
Shoddy safety standards notwithstanding, the film says the gyrospheres are designed so visitors can get close to the dinosaurs without facing any danger, since the glass frames can stop a 50-caliber bullet and protect visitors from some of these reptiles’ venomous spit. (Fun fact: For filming, these vehicles weren’t just CGI’ed – they were built and rolled onto a track on ball bearings).
Despite the durability claims, as we can see in this scene, the Indominus Rex gets hold of Ben and Kenji and pierces the capsule’s glass with a tap of its talon. Moments later, the boys escape before the dinosaur smashes the vehicle into bits with its mighty jaws.
With the help of Irazu software by Geomechanica, we investigated how much force you’d need to break the gyrosphere’s thick glass in the real world. We wondered, Would the force of Indominus’ giant claw actually be enough to break the glass, or did the movie ignore the physics and let the special effects team take the lead? We decided to put this to the test.
Irazu software specializes in rock mechanics studies, and since glass possesses similar brittle fracturing properties as rock, the software was the perfect choice to carry out our simulations.
Simulating the Gyrosphere
The team began by building a 3D model of the spherical gyrosphere. Given the symmetry of the problem, only half of the spherical glass gyrosphere was modeled as a hollow hemisphere with its outer diameter equal to 1 meter and a thickness of 10 centimeters. The team also incorporated a 2-centimeter thick layer of polymeric material to better represent the laminated structure of the bullet-resistant glass. The team also incorporated a single claw of the Indominus Rex into the model, represented by a 10-centimeter-long truncated cone with an upper and lower diameter equal to 4 centimeters and 1.7 centimeters, respectively.
The model geometry was discretized by a tetrahedral finite element mesh (approximately 80,000 elements in total) having the finest spatial resolution (2 millimeters) in the area around the tooth-hemisphere contact. The bone, glass, and polymer materials were modeled as brittle, isotropic solids and assigned suitable stiffness and strength property values. The violent swipe of the Indominus Rex was captured by prescribing a velocity of 0.5 meters/s to the claw in the direction orthogonal to the hemisphere surface.
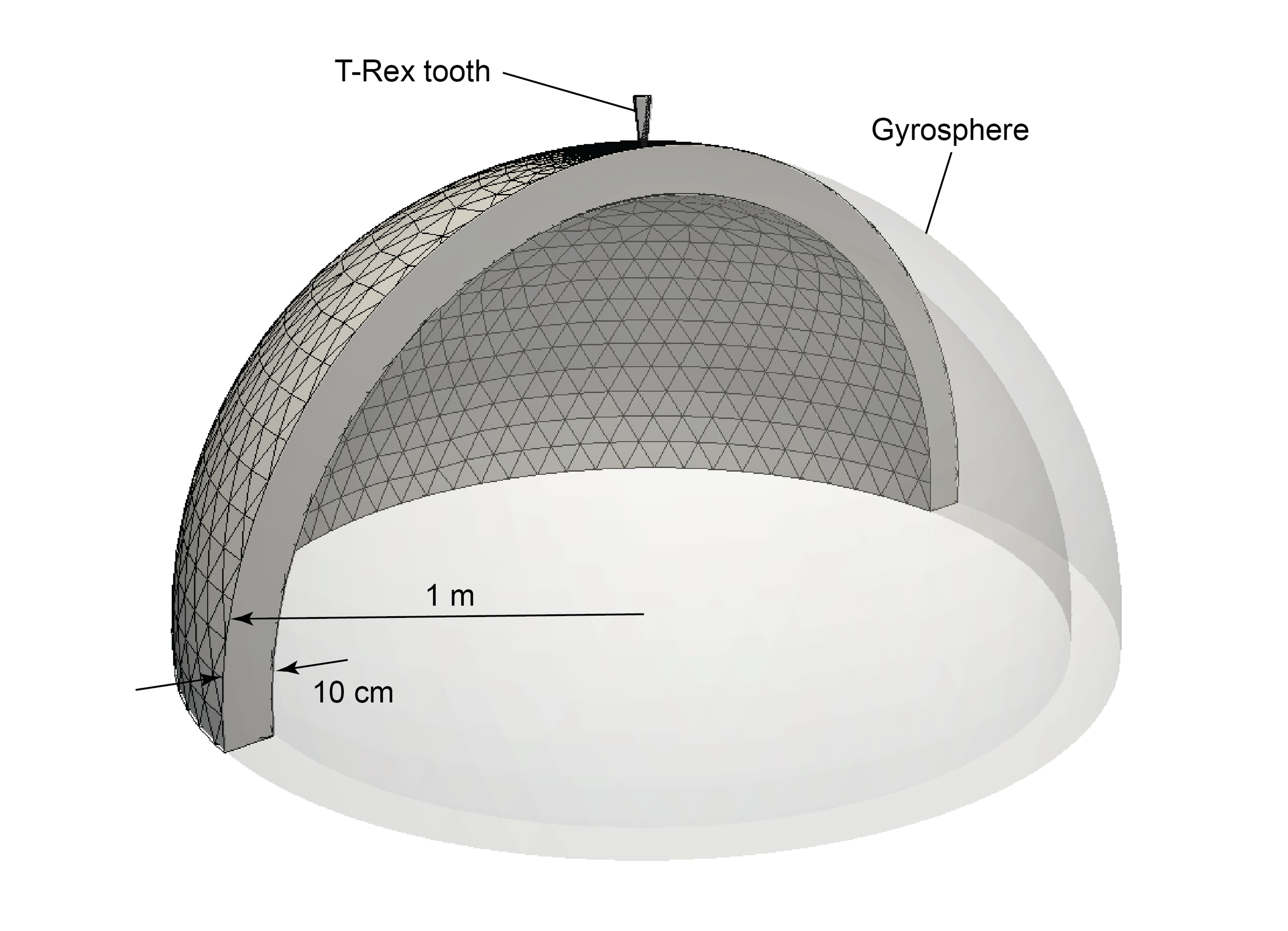
Results
The gyrosphere glass’s simulated fracturing under the effect of the Indominus Rex’s claw is highlighted in the model animations below. Once the claw comes in direct contact with the glass, the glass starts to fail; the fracturing moves downwards as a cone-shaped fractured volume. Under increasing pressure, tensile fractures nucleate and grow from the inner surface of the gyrosphere. Finally, a cone-shaped piece of glass completely detaches on the inside of the gyrosphere and is ejected towards the center (spalling).
The gyrosphere glass begins to crack and break as pressure from the Rex claw increases. The gyrosphere glass begins to crack and break as pressure from the Rex claw increases.
We derived the force required to break the bullet-proof glass from the analysis of the reactionary forces acting on the claw as a function of the penetration of the claw into the gyrosphere. The model below shows the glass fracturing and detaching under immense stress.
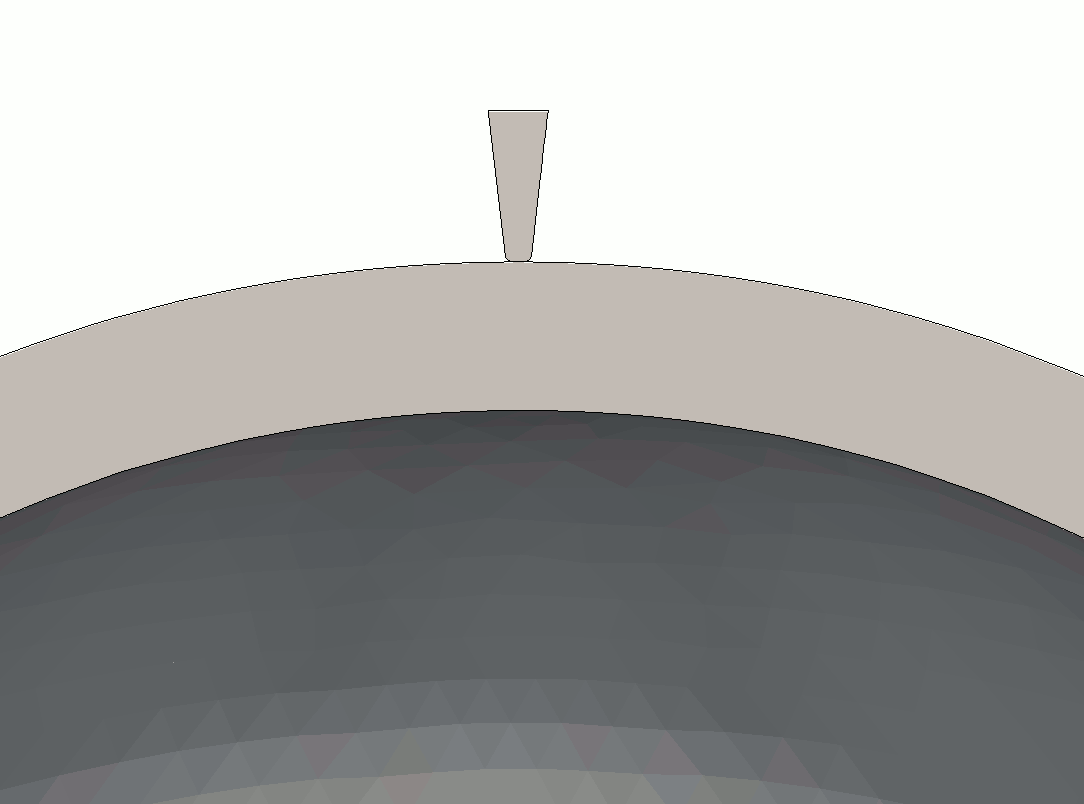
And as shown in the graph below, a peak applied load of 2,800 kN (285 ton) was recorded, thus corresponding to the value required to break the glass.
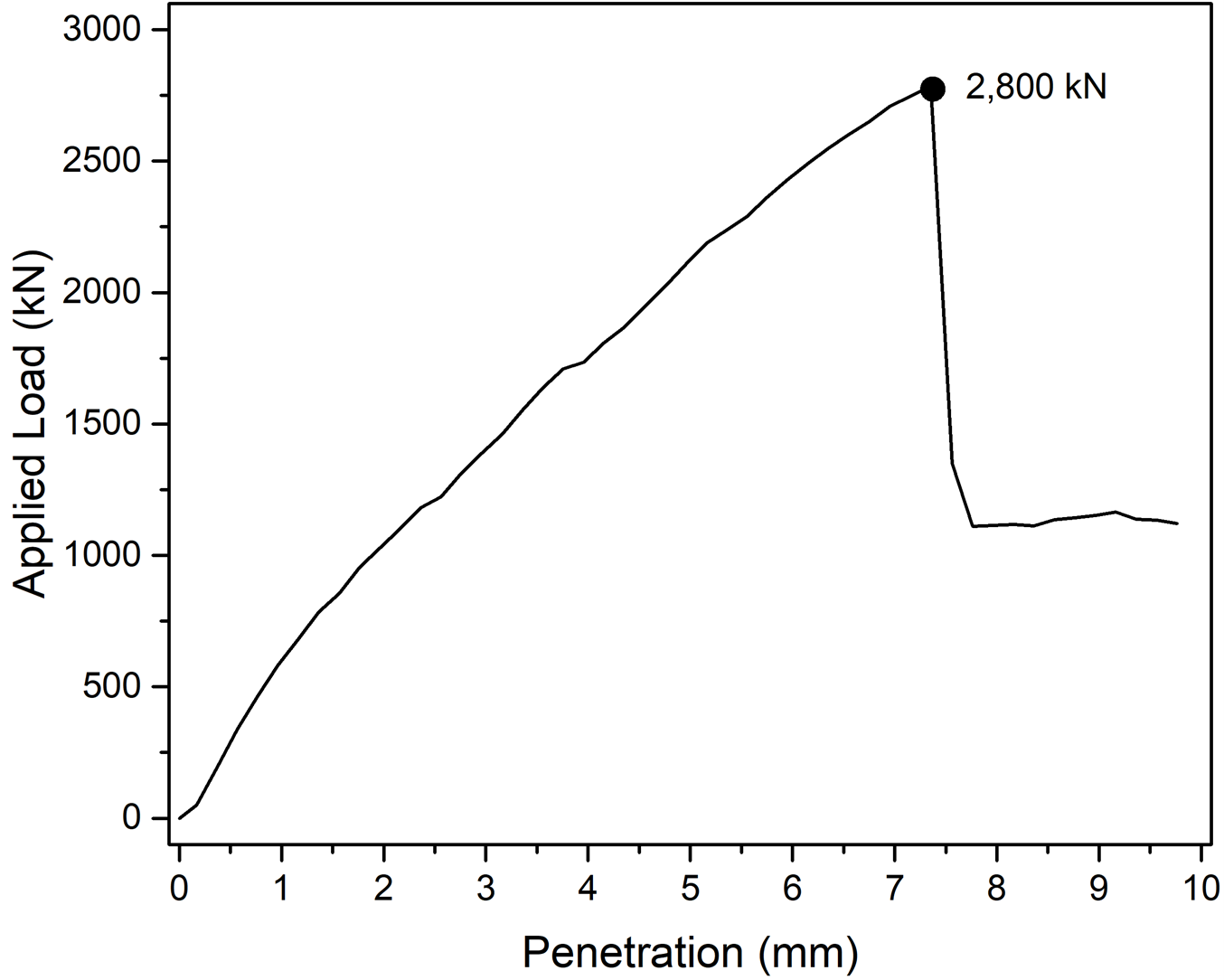
To put that load recording into perspective, a typical hydraulic press used in rock mechanics testing labs have a capacity of 1300 kN. This would mean that the Indominus Rex’s talon tap would, in theory, need to deliver two times the power of an industrial mining hydraulic press to break through the high-strength glass.
So could a dinosaur exert this much force from a swipe of its claw? Since there are no longer any real-life dinosaurs to test our hypothesis with (which is probably for the best), it’s impossible to know for sure. But we don’t think even the most powerful dinosaur could exert the rock-pulverizing power of modern mining equipment. Although the Indominus Rex undoubtably packs a punch, it probably couldn’t destroy a gyrosphere. Regardless, I don’t plan on perusing a field of dinosaurs in one anytime soon – I’d rather this experiment remain hypothetical.
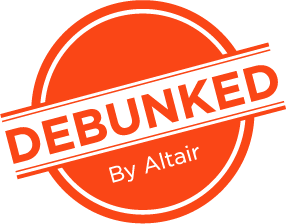
About Geomechanica
Geomechanica, part of the Altair Partner Alliance, solves challenging rock mechanics problems through the development and application of state-of-the-art numerical simulation methods. Creating solutions for industries such as civil engineering, mining, and petroleum engineering and research, users can create customized simulations and run analyses using the Irazu software solver technology.
With the ability to simulate deformation, fracturing, and coupled processes in rock masses, Irazu offers designers the computational power to simulate at a higher fidelity with GPU computing. With the higher power comes less of a need for designers to make inaccurate modeling assumptions on designs.
The integration of various multi-physics solvers and advanced features into a single software package enables Irazu to be used for a wide range of engineering applications, including but not limited to excavations, slope stability, tunnelling, dynamic analysis, mining, and reservoir geomechanics. The technology serves as an all-in-one simulation tool for design and analysis of a wide range of geo-engineering applications.
If you’re interested in learning more about using geomechanical analysis in mining applications, check out the webinar below featuring Ove Arup & Partners, Altair, and Geomechanica.