Holistic Carbon Footprint Assessment and Reduction
Are you wondering how green your product is, and do you need to accurately measure and monitor its carbon footprint going forward?
Because of a myriad of new legal requirements, many of today’s companies must use a certain proportion of recycled material in their final products. As such, they need to ensure the quality of the final product despite fluctuating or unknown material properties. In addition, they must provide evidence of the product’s actual carbon footprint.
What if you could evaluate and document the actual carbon footprint of your product in a way that considered all energy contributions due to the processing steps? And imagine all that could happen in a simple, automatic manner – how can this vision become reality?
This can be possible when the CO2 information of the starting materials, additives, and/or recyclable materials are available, and when users can undertake a continuous digital mapping of the individual energy inputs along the processing journey.
With material handling, mixing, drying, compounding, and injection molding, there are energy expenditures that must be allocated to the final product in the form of a CO2 footprint. Each step of the process requires precise operational parameters, which must be adjusted depending on the environmental conditions and the properties of the processed material. If users can capture the process’s energy demands and align that information with material-specific process parameters, users can identify and optimize inputs and processing.
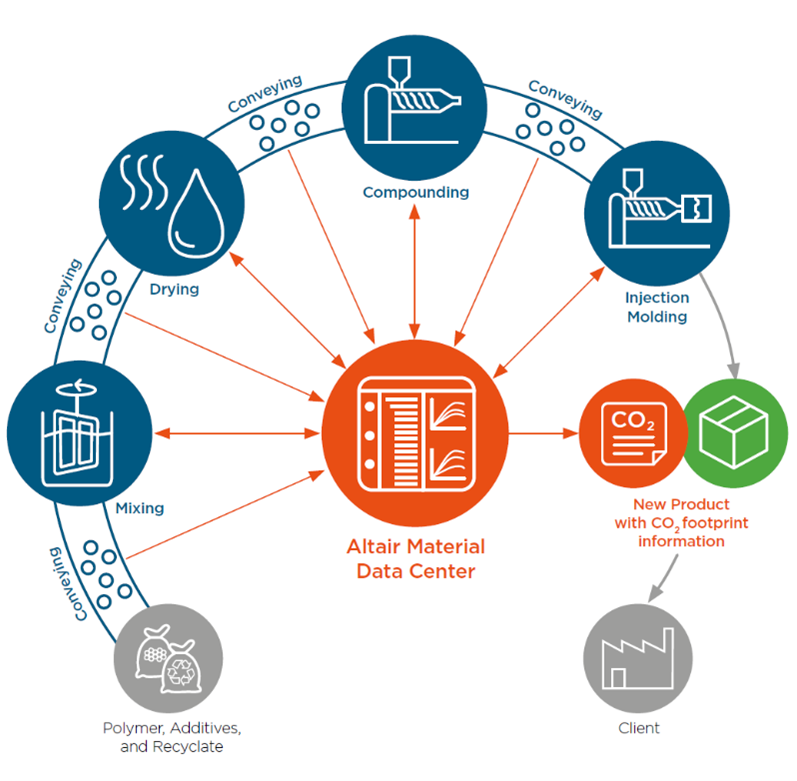
“The assessment of the CO2 balance is essentially an information problem that the motan-Altair CO2 Tracker technology demonstrator addresses,” said Dr. Laura Thurn, material engineering manager, Altair.
The CO2 Tracker Concept
The motan Group, which is headquartered in Constance, Germany, is a market-leading technology provider of equipment and systems for the plastics manufacturing and processing industry. motan drives the constant change and further development of the plastics industry and pursues the principle to grow through innovation.
Plastics processing companies need up-to-date, relevant material data alongside up-to-date process parameters. This is where motan and Altair’s technology comes into play, which we’ll call the “CO2 Tracker.” Altair provides the necessary data infrastructure and basic material information via a material database, and motan complements and networks the material logistics including the machines involved for conveying, processing, drying, and compounding. For each step, the CO2 Tracker determines, records, and aggregates the energy consumption. From there, this data is fed back into the material database so users can analyze and visualize it.
The background database system is an individual version of the Altair Material Data Center, in which the existing material data is supplemented with properties related to the CO2 balance and the processing properties. Via an interface to the motan Material Data Gateway, Altair supplies the motan server with the corresponding processing data, which then provides information about new and processed batches. This data is then visible and managed at a desired location to improve decision-making, process flows, and products.
Altair complements the material flow along the processing chain with a continuous flow of information. By recording and documenting processing parameters and energy inputs through material handling, the manufacturing data of the material is completed.
Such a system-supported workflow increases material data transparency and expands the material competence of companies. The resulting digital twin of the material helps users make future decisions regarding product design and processing optimization. As a result, users can derive recommendations for optimal processing, and minimize waste, material, and energy losses.
“The CO2 Tracker project from motan and Altair is the first integrated approach to map the complete production process and provides true material data transparency by capturing the actual processing data,” said Sandra Füllsack, chief executive officer, motan Group.
To learn more about the collaboration between Altair and motan and explore the CO2 Tracker’s capabilities further, visit https://web.altair.com/altair-at-k2022.