How Simulation Addresses GM’s Biggest Hurdles in Electric Car Adoption
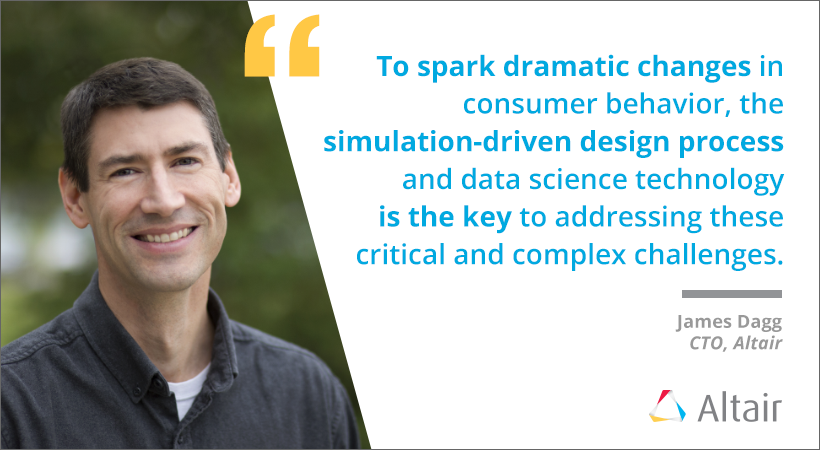
Recently, the president of General Motors wrote a perspectives article for CNN Business outlining the automotive industry’s most pressing challenges that stand in the way of mass adoption of electric cars.
Carmakers around the world have made massive investments in drivetrain electrification, but it will take more than incremental performance improvements to shake up the status quo and move the masses away from internal combustion engines. To spark dramatic changes in consumer behavior, the simulation-driven design process and data science technology is the key to addressing these critical and complex challenges.
Let’s break down the three challenges he outlined one-by-one.
Range
In order to get the most mileage out of each charge, manufacturers are turning to simulation technology to reduce vehicle weight, improve energy efficiency and optimize the next generation of electric motors.
Lighter cars require less battery power for accelerating and maintaining speed, allowing a single charge to take passengers further. Generative design techniques enable engineers to remove material from the structure and individual components, all while maintaining the strength and stiffness properties required for vehicle safety and ride comfort. Removing weight from the structure also has compounding benefits. Since less power is required for propulsion in lighter vehicles, carmakers can reduce the size and weight of the battery packs, which are one of the biggest contributors to an electric car’s weight.

Energy efficiency is also a key contributor to vehicle range improvement. Computational fluid dynamics (CFD) is being introduced early in the design process, allowing aerodynamic properties to influence the shape and styling of the outer surfaces of the vehicle. Additionally, CFD can be used to investigate and optimize the thermal management of the electrical and mechatronic systems to avoid performance issues caused by overheating.
Finally, there’s improving the electric motor itself. To account for the complexities of designing powertrain systems, companies like Porsche deploy a multiphysics design strategy, including electromagnetics and thermal requirements, NVH, stress and durability. The results feed design exploration and optimization studies to identify the motor designs that will yield the best performance.
Charging infrastructure
According to a study by Statista, there were more than 100,000 retail gas fueling sites in the United States as of 2016. By comparison, a second study by Statista reports that as of 2018 there were just 20,000 charging stations for plug-in electric vehicles in the U.S. This represents a major potential disruption for EV drivers looking to venture outside of their typical commuting range. A substantial commitment is needed from a collaboration of private and government institutions to build an adequate electric vehicle charging infrastructure, but software technology provides optimism this is achievable soon.
Data science, artificial intelligence and machine learning algorithms can be used to map optimal routes for drivers to take advantage of existing charging infrastructure. Data science also enables manufacturers, charging companies, industry groups and governments to make data-driven urban planning decisions that prioritize the construction of new charging infrastructure based on real-time traffic flow patterns and vehicle range data.
Finally, simulation is being used to develop innovative new ways of charging vehicles, making it easier for drivers to charge their batteries at home and on the go. Gulplug, a startup from France, created a self-plugging magnetic charging solution that both assists drivers with the task of charging and opens the door for autonomous vehicles to park and charge themselves without any human intervention.
Autonomous connection and contact-less charging solutions may even reduce the need for dedicated charging infrastructure, making fueling stations a thing of the past.
Cost
Perhaps the most direct barrier to entry for most consumers is the cost of an electric vehicle. Lightweighting, in addition to improving battery range, provides cost benefit through material reduction. Improvements to electric motor efficiency also helps manufacturers reduce battery sizes to furthering the cost reduction.
Mercedes-AMG and other OEMs leverage representative system models throughout various stages of their design process, helping to accelerate design delivery, and evaluate efficiency and performance. This in-depth understanding of complex mechatronic systems helps manufacturers push new products to market faster, with fewer costly physical prototypes.
It may be difficult for some consumers to envision themselves driving an electric car, and the uphill battle outlined in the CNN article demonstrates these challenges, but with modern simulation and data science tools within reach, the outlook for an electrified future looks brighter than ever.
Interested in working with Altair on your next electric mobility project? Contact us today.