Strong and Lightweight: The Best of Both Worlds in Racing
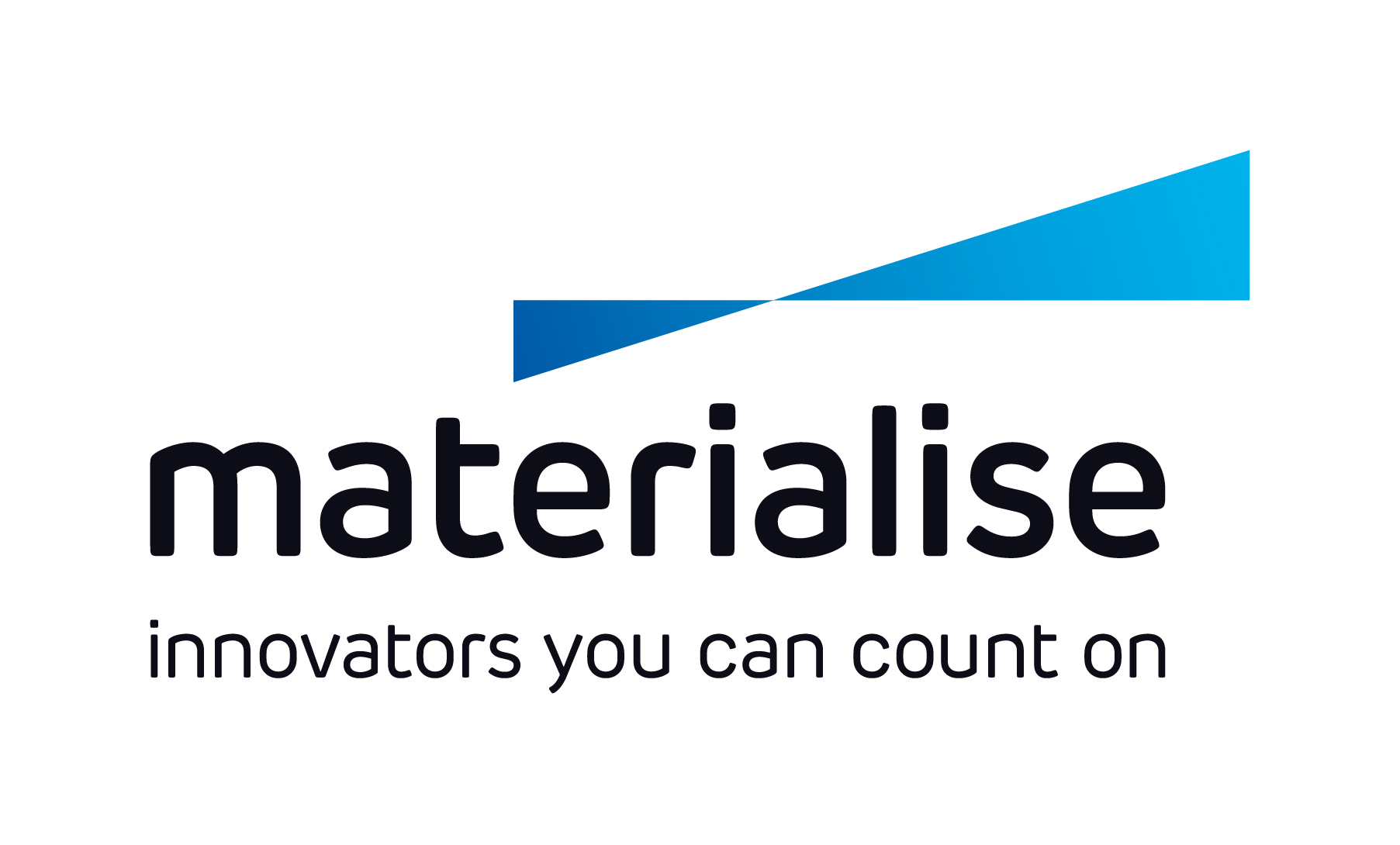
This guest contribution on Innovation Intelligence is written by Kirsten Van Praet and Mariam Mir, Sales & Marketing at Materialise. Materialise 3-matic is available through the Altair Partner Alliance.
Every two years, the World Solar Challenge attracts students and private entrepreneurs from all over the world to cross Australia with their custom built solar cars. In order to beat the other race cars, the solar car needs to be as light as possible – this is a great way to stimulate research on solar energy. The Belgian team, made up of students at the KU Leuven University, reached a whopping 90 km per hour (or 56 miles per hour) on average, which beats the record of all previous Belgian solar teams that participated in the event. One of their secret weapons? An inventive battery structure, created with Materialise 3-matic software.
Strong, Compact and Light: A Battery Structure Born to Race
When participating in a race, the weight of your car is a key component that will determine your success. That’s why the race car team collaborated with Materialise to develop an optimized battery structure that should be aerodynamic, compact, light and strong. To spread the heat in an optimal way, it should also be porous. Sounds like the perfect job for design enhancement software, Materialise 3-matic.
With Materialise 3-matic the designers applied a porous structure on the design, resulting in a light yet strong model using only the minimal necessary material. In this way, the batteries could be contained in an optimal structure. Afterwards, the printability of the design was verified in Materialise Magics. Wall thickness and other technical features were checked to make sure that the part would print problem-free on one of Materialise’s laser sintering machines.
In addition to the battery pack, the Battery Monitoring System (BMS) pack was also 3D-printed after design enhancement and file preparation in Materialise 3-matic and Materialise Magics, respectively.
“Because of the lattice structures, the battery pack design was a very heavy file,” explains Dries Vandecruys, Design Engineer at Materialise. “That’s not a problem for advanced software like Materialise 3-matic. It makes the big data easy to work with.”
Speed and Energy Efficiency
The Belgian solar team ended in the fifth position, with a race car that had reached up to 110 km per hour (or about 68 miles). If it wasn’t for one hour lost to repairs, and another because of a time penalty, the team had potential to reach the finish line first.
“In terms of speed and energy efficiency, our car performed even better than we had hoped for,” the KU Leuven team explained. “We ended 1 hour and 23 minutes behind the winner, the Nuon Solar Team. Compared to the previous race in 2013, where we ended 7 hours behind the winner, it is a huge step forward.”
Read more Materialise case studies to find out how other automotive companies and other industries apply Materialise 3-matic.