Quantification of Metal Flow Lines
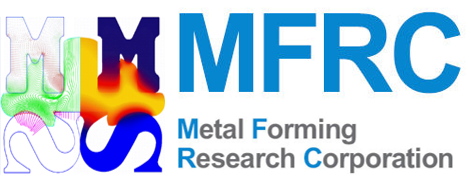
The design of a manufacturing process is iterative in nature. The influential process parameters which can be quantified (E.g. Die radius) are continuously optimized using metal forming simulators coupled with optimization algorithms. This approach is being successfully applied at various levels of process design, but it has a limitation. The qualitative parameters have a significant impact on the process and they get excluded. For example, metal flow lines.
In metal forming, especially in forging, metal flow lines formed during rolling or drawing play a decisive role in determining the strength of a product. S. Ito et al. [1] observed that an optimal distribution of metal flow lines can increase the lifespan of mechanical and automotive parts by nearly six times.
These metal flow lines store the history of the metal formed products and are being utilized for qualitatively evaluating product quality and durability of power transmission or load supporting parts like bearings and gears. But, qualitative evaluation effectively means that one must depend on his/her experience to decide on the worthiness of the process. This becomes an obstacle if one would like to optimize the process design using a metal forming simulator. In other words, it was not possible to treat metal flow lines directly as an objective function or a constraint while defining a process design optimization problem.
To address this issue, AFDEX developers have recently developed (and patented) a method to quantify the metal flow lines in terms of quality indices which includes a density function of metal flow lines as well as its overlapping index (See Figure 2). The overlapping of metal flow lines can be prevented by minimizing or controlling this index. The same approach can be applied to 2D as well as 3D problems.
The core idea is to use these indices which quantify metal flow lines as constraints or objective functions in an optimization problem in addition to other commonly used die design parameters.
As the quality of metal flow lines have a noteworthy influence of the life span of the part, the optimization of process design should be carried out also based on the high quality of metal flow lines rather than just the forming load. With the availability of state-of-the-art metal forming simulation technology and optimization algorithms (AFDEX and Altair HyperStudy respectively), this approach will be very valuable for manufacturers to stay ahead of competition.
This white paper is a good starting point to learn more about using AFDEX and HyperStudy for metal forming process design optimization.
References:
[1] S. Ito, N. Tsushima, H. Muro, 1982, Accelerated rolling contact fatigue test by a cylinder-to-ball, Rolling contact fatigue testing of bearing steel ASTM STP 771, American Society for Testing and Materials, pp. 125-135.
This guest contribution on Innovation Intelligence is written by Renganathan Sekar, M.Sc., researcher at MFRC, the developers of the intelligent metal forming simulation software AFDEX which is available through the Altair Partner Alliance.
In metal forming, especially in forging, metal flow lines formed during rolling or drawing play a decisive role in determining the strength of a product. S. Ito et al. [1] observed that an optimal distribution of metal flow lines can increase the lifespan of mechanical and automotive parts by nearly six times.
These metal flow lines store the history of the metal formed products and are being utilized for qualitatively evaluating product quality and durability of power transmission or load supporting parts like bearings and gears. But, qualitative evaluation effectively means that one must depend on his/her experience to decide on the worthiness of the process. This becomes an obstacle if one would like to optimize the process design using a metal forming simulator. In other words, it was not possible to treat metal flow lines directly as an objective function or a constraint while defining a process design optimization problem.
To address this issue, AFDEX developers have recently developed (and patented) a method to quantify the metal flow lines in terms of quality indices which includes a density function of metal flow lines as well as its overlapping index (See Figure 2). The overlapping of metal flow lines can be prevented by minimizing or controlling this index. The same approach can be applied to 2D as well as 3D problems.
The core idea is to use these indices which quantify metal flow lines as constraints or objective functions in an optimization problem in addition to other commonly used die design parameters.
As the quality of metal flow lines have a noteworthy influence of the life span of the part, the optimization of process design should be carried out also based on the high quality of metal flow lines rather than just the forming load. With the availability of state-of-the-art metal forming simulation technology and optimization algorithms (AFDEX and Altair HyperStudy respectively), this approach will be very valuable for manufacturers to stay ahead of competition.
This white paper is a good starting point to learn more about using AFDEX and HyperStudy for metal forming process design optimization.
References:
[1] S. Ito, N. Tsushima, H. Muro, 1982, Accelerated rolling contact fatigue test by a cylinder-to-ball, Rolling contact fatigue testing of bearing steel ASTM STP 771, American Society for Testing and Materials, pp. 125-135.
This guest contribution on Innovation Intelligence is written by Renganathan Sekar, M.Sc., researcher at MFRC, the developers of the intelligent metal forming simulation software AFDEX which is available through the Altair Partner Alliance.