Quit Your Batching – How Smart Technology Can Make Continuous Manufacturing a Reality
In recent years, advances in manufacturing processes and smart technology has allowed many industries to transition from batch-based processing to continuous manufacturing systems, leading to higher output volume and larger profit, reduced manpower dependency, and better quality control. While both batch and continuous manufacturing serve specific applications, the ubiquity of smart technologies and its proliferation into industry has made it easier to implement a continuous system, leading many companies to explore what is now possible. For example, given that the pharmaceutical industry loses about $50 billion a year because of the general inefficiencies of batch processing, continuous manufacturing can be a potential solution that could save considerable time and money. But what are these smart technologies and how do they make continuous manufacturing a reality?
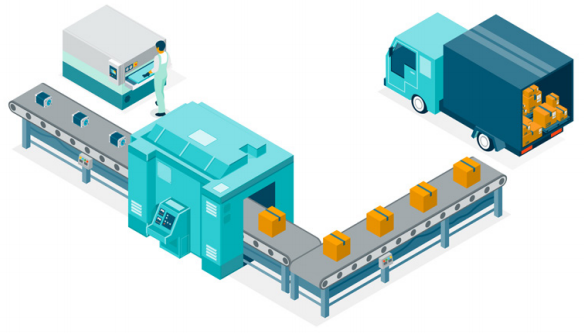
Batch vs. Continuous Manufacturing
Generally speaking, a batch process is one that consists of one or more steps performed in a defined order, resulting in a finite amount of product at the end of the sequence. Because of the nature of batch processing, it can be controlled very easily by a small workforce. The downside of batch processing is wastage as a result of quality issues that go unnoticed until the entire batch is produced.
On the other hand, continuous manufacturing involves the constant processing of a material or mixture, with every machine operating in a steady state. This method saves time, reduces the likelihood for human error, and can respond more nimbly to market changes. Additionally, the continuous output ensures that corrective action is taken as soon as a quality defect is identified.
While an ‘always on’ approach leads to a higher product yield and increased profits, it is necessary to ensure the system in place will function correctly over long stretches of time and therefore requires a thorough knowledge of the demands that system will face. The emphasis to get it right the first time is a driving force of the movement, and so there is a higher reliance on accurate simulation models and smart manufacturing technologies.
How Smart Technologies can help with Continuous Manufacturing
This is where smart technologies can help. Digital twins help organizations optimize product performance, gain visibility into the in-service life of a product, know when and where to perform predictive maintenance, and understand how to extend a product’s remaining useful life (RUL). This can be an incredibly useful tool in process manufacturing, especially considering the demanding methods such as continuous manufacturing or the potential cost savings of implementing such a tool.
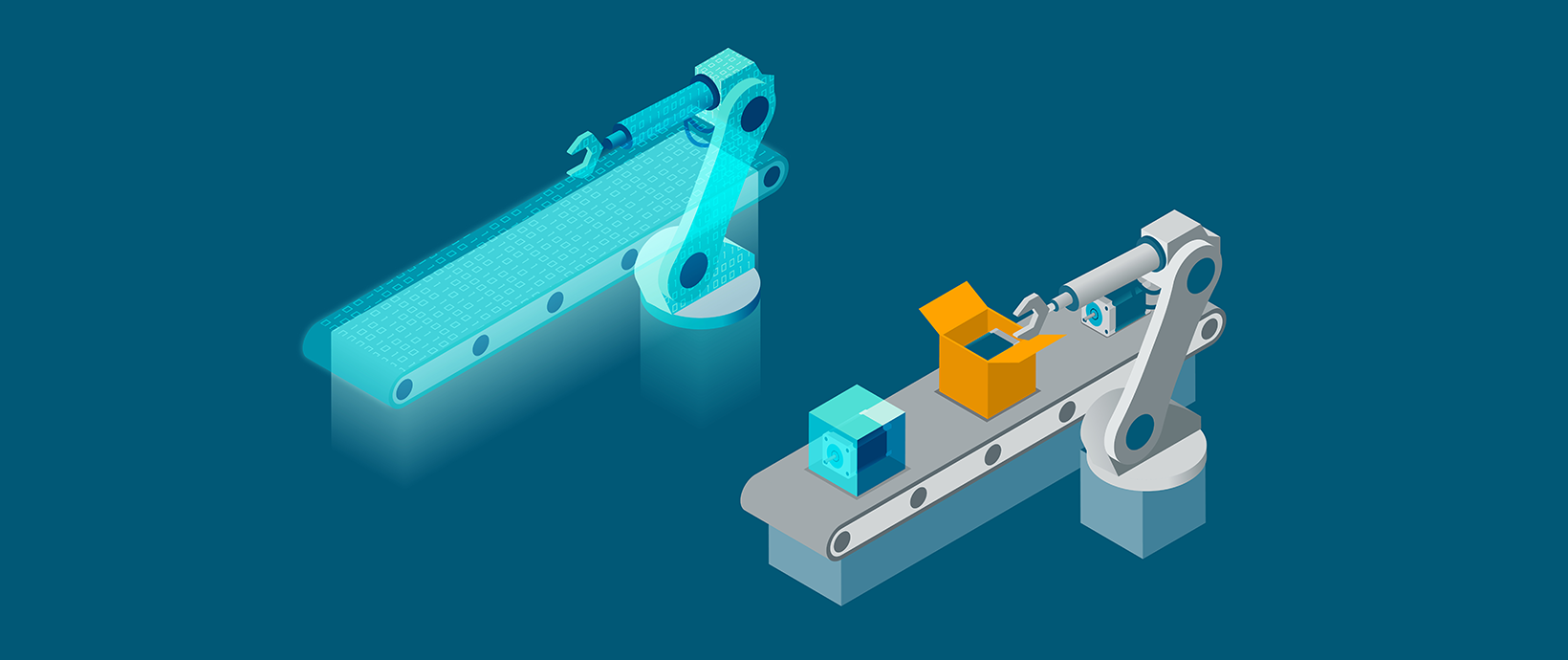
Numerical modeling software such as Altair EDEM™ can be incorporated into the digital twin model to simulate processes common in continuous manufacturing such as mixing and coating. Companies can rely on operational data streamed from equipment as an input to the digital twin model, helping them to predict when maintenance is required to keep that machine running, leading to a more efficient maintenance process with more consistent uptime. For example, the use of vibration sensors can provide an alert when motors, bearings, or other equipment begin to falter and require maintenance. Additionally, real-time data streaming and the ability to change system parameters to simulate their impact on quality are advantages that smart technologies bring to continuous manufacturing.
Data collected across the process can also be used to identify bottlenecks. Traditional approach involves manually analyzing different systems and processes to uncover inefficiencies, often difficult to identify at all. By tracking the data produced in real time, inefficiencies and bottlenecks that are usually unnoticed become obvious. Artificial intelligence and machine learning algorithms that can review large amounts of data in real time discover anomalies and correlate them to detrimental events. All of this goes towards building an effective continuous manufacturing process.
To learn more about the use of continuous manufacturing in the pharmaceutical industry, check out this virtual panel presentation by Dr. Fernando Muzzio of Rutgers University, a renowned expert on pharmaceutical part and process design. In it, he discusses his research on manufacturing process improvement, leveraging continuous manufacturing and discrete element method modeling together to optimize functions such as pharmaceutical formulation, powder mixing, capsule filling, and tablet coating.